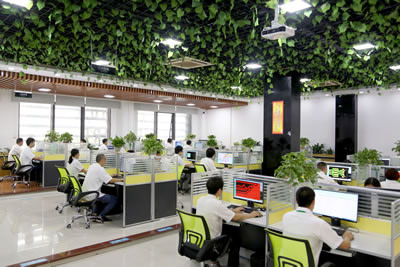
QUALITY ASSURANCE
Quality starts with our first conversation with a customer. We take the time to understand your business and requirements and we apply our quality control across all our processes from order to delivery – and on-wards.
Our Global QA team reports on:
MARKET ACCREDITATIONS
We support specific market applications across automotive, medical, rail and aerospace markets:
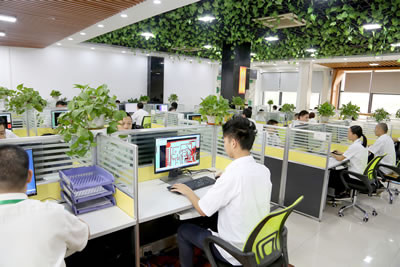
Introduction and control of new SMT models
1. To arrange a pre-trial production meeting with the production department, quality department, process and other relevant departments before the trial production, mainly to explain the production process of the trial production model and the quality key points of each station.
2. The manufacturing department arrange the production line for trial production according to the production process or the engineers’ plan. The processes engineers of each department should follow up on the line, deal with the abnormalities in the trial production process in a timely manner and record them.
3. The quality department should check the First-piece and test the performance and functionality of the trial production model, and fill in the corresponding trial production report (the trial production report will be sent to our engineer department by email ).
The ESD controls in SMT
1. Requirements for the processing area: the warehouse, stickers, and handle soldering workshops should meet the requirements of the ESD control, the ground is laid with anti-static materials, the processing table is laid with anti-static mats, the surface impedance is 104-1011Ω, and the electrostatic grounding buckle (1MΩ±10%);
2. Requirements for the people: Should wear the anti-static clothing, shoes and hats when entering the workshop, and wear a corded electrostatic ring when contacting products;
3. The rack for moving , the foam for packaging, and the bubble bag need to meet the ESD requirements, and the surface impedance < 1010Ω.
4. The rotating plate frame should be connected to an external chain to achieve grounding;
5. The leakage voltage of the equipment <0.5V, the impedance to the ground <6Ω, the impedance of the soldering iron to the ground <20Ω, and the equipment needs to evaluate the external independent grounding wire;
The MSD controls in SMT
1. The pins’ encapsulation material for BGA and ICs are easy to be damp under non-vacuum (nitrogen) packaging conditions, moisture volatilization when SMT reflux, causing soldering abnormality, it need to be 100% baking.
2. BGA Regulatory Specifications
(1) Vacuum-packed unopened BGAs must be stored in an environment with a temperature lower than 30°C and a relative humidity of less than 70%, and the service life is one year.
(2) The unpacked BGA must be marked with the unpacking time, and the unpacked BGA should be stored in a moisture-proof cabinet under ≤ storage conditions of 25°C, 65%RH, and the storage period is 72hrs.
(3) If the BGA has been opened but has not been used online or the remaining material must be stored in a moisture-proof box (condition≤ 25°C, 65%R.H.) If the BGA returned to the large warehouse is baked by the large warehouse, the large warehouse will be stored in vacuum packaging.
(4) If the storage period is exceeded, it must be baked at 125°C/24hrs, and if it cannot be baked at 125°C, it must be baked at 80°C/48hrs (if it is baked multiple times, the total baking hours must be less than 96hrs) before it can be used online.
(5) If the components have special baking specifications, they will be ordered into SOP.
3. The PCB storage cycle > 3 months, and it needs to be baked at 120°C 2H-4H.
The PCB Regulatory Specification in SMT
1. PCB unpacking and storage SMT
(1) The PCB board is sealed, unopened, and can be used directly within 2 months from the date of manufacture.
(2) The date of manufacture for the PCB board is within 2 months, and the date of unpacking must be marked after unpacking.
(3) The manufacturing date of the PCB board is within 2 months, and it must be used online within 5 days after unpacking.
2. PCB baking SMT
(1) If the PCB is sealed and unpacked for more than 5 days within 2 months of the date of manufacture, please bake at 120 ±5°C for 1 hour.
(2) If the PCB is more than 2 months past the manufacturing date, please bake at 120 ±5°C for 1 hour before going online.
(3) If the PCB is 2 to 6 months past the manufacturing date, please bake at 120 ±5°C for 2 hours before going online.
(4) If the PCB exceeds the manufacturing date for 6 months to 1 year, please bake at 120 ±5°C for 4 hours before going online.
(5) The baked PCB must be used within 5 days, and the bit must be baked for another 1 hour before it can be used online.
(6) If the PCB exceeds the manufacturing date for 1 year, please bake at 120 ±5°C for 4 hours before going online, and then send it to the PCB factory to re-spray tin before it can be used online.
3. Storage period of IC vacuum sealed SMT packaging:
(1) Please pay attention to the sealing date of each box of vacuum packaging;
(2) Shelf life: 12 months, storage environmental conditions: at a temperature of < 40 °C, humidity = "">< 70% = "" r.h;="">
(3) Check the humidity card: the displayed value should be less than 20% (blue), such as > 30% (red), which means that the IC has absorbed moisture.
(4) If the unpacked IC component is not used up within 48 hours: if it is not used up, the IC component must be re-baked when it is launched for the second time to remove the moisture absorption problem of the IC component;
(4.1) High temperature resistant packaging material, 125°C(±5°C), 24 hours;
(4.2) Non-high-temperature resistant packaging material, 40°C (±3°C), 192 hours;
Unused items should be put back in the drying oven for storage.
The Bar code control in SMT
1. Corresponding orders, our company will send matching bar code stickers, bar codes are controlled in accordance with the orders, and no omissions or mistakes can be pasted, and abnormalities will be tracked;
2. The bar code is attached to the reference sample to avoid mixing and missing paste, and the bar code should not cover the pad.
If the area is insufficient, please feedback to our company for adjusting the location.
The Report control in SMT
1. The process, testing, and maintenance of the corresponding model must be controlled by making reports, and the content of the report includes (serial number, defective problems, time period, quantity, defective rate, cause analysis, etc.) for easy tracking.
2. When the same problem occurs in the production (test) process of the product is as high as 3%, the quality department have to ask the engineer to improve and analysis it’s reasons, and continue producing only after confirmation.
3. At the end of each month, our suppliers will count the process, testing and maintenance reports and sort out a monthly report and send it to our company by Email for quality and process department.
The Solder paste Printing control in SMT
1. The solder paste should be stored within 2-10 °C, and used according to the first-in-first-out principle, and controlled by control-labels; the unopened solder paste should not be stored for more than 48 hours at room temperature, and the unused solder paste should be returned to the refrigerator for refrigeration in time; the opened solder paste should be used up within 24 hours, and the unused solder paste should be put back into the refrigerator for storage and recorded in time;
2. The screen printing machine is required to folded the solder paste on both sides of the squeegee every 20min, and a new solder paste should be added every 2-4H;
3. The first piece of mass production silk screen printing takes 9 points to measure the thickness of the solder paste, and the tin thickness standard: the upper limit, the thickness of the steel mesh + the thickness of the steel mesh * 40%, the lower limit, the thickness of the steel mesh + the thickness of the steel mesh * 20%. If the fixture is used for printing, the fixture number is indicated on the PCB and the corresponding fixture, so that it is easy to confirm whether the fixture causes the defect when there is an abnormality. The temperature data of the reflow soldering test furnace is transmitted back to ensure that it is transmitted at least once a day. The tin thickness is controlled by SPI, which requires that it be measured every 2 hours, and the appearance inspection report after the furnace is transmitted once every 2 hours, and the measurement data is transmitted to our company's process department;
4. If the printing is poor, please use a dust-free cloth to wash the board in order to clean the solder paste on the surface of the PCB, then use an air gun to clean the residual tin powder on the surface;
5. Self-check whether the solder paste is biased and tin tip before placement, if the printing is poor, the cause of the abnormality should be analyzed in time, and the abnormal problem points should be checked after adjustment.
The mounting control in SMT
Components checking: To check whether the BGA and IC are vacuum-packed before going online, if it is not vacuum-packed, please check the humidity indicator card to see if it is wet.
1. When loading, please check the station according to the feeding table, check whether there is any wrong material, and do a good job of feeding registration;
2. Placement procedure requirements: please pay attention to the accuracy of placement.
3. To self-check whether there is any deviation after the sticker;
4. The corresponding model SMT needs to be took 5-10 pieces of IPQC to DIP and wave solder every 2 hours , do ICT (FCT) function test, and mark it in PCBA after the test.
The Reflow control in SMT
1. In the case of overflow soldering, set the furnace temperature according to the maximum electronic components, select the temperature measuring plate of the corresponding product to test the furnace temperature, and import the furnace temperature curve to see whether it meets the requirements of lead-free solder paste soldering.
2. Use lead-free furnace temperature, and control each section as follows:
Heating rate: 1°C ~ 3°C per second;
Cooling rate: 1°C ~ 4°C per second;
Constant temperature phase: keep the temperature between 150°C and 180°C for a duration of 60 seconds to 120 seconds;
Temperature above melting point: Keep above 220°C for a duration of 30 seconds to 60 seconds to ensure that the material melts.
3. The product interval is more than 10cm to avoid uneven heating and virtual welding.
Do not use the card board to place the PCB to avoid collisions, and need to use a turnover car or anti-static foam;
Appearance inspection of SMT patches
1. BGA needs to take X-RAY once every two hours to check the welding quality, and check whether other components are offset, less tin, bubbles and other welding defects, and the technical staff needs to be notified to adjust if they appear continuously in 2PCS.
2. BOT and TOP surface must pass AOI inspection and quality inspection.
3. Inspect defective products, use defective labels to mark the defective location, and place them in the defective product area, and the on-site status is clearly distinguished.
4. The yield rate of SMT stickers is required to be > more than 98%, and if there is a report that exceeds the standard, it is necessary to open an abnormal order for analysis and improvement, and there is no improvement for 3H and the shutdown is rectified.
The Post-soldered in SMT patch
1. The temperature of lead-free solder furnace is controlled at 255℃-265℃, and the minimum value of solder joint temperature on PCB board is 235℃.
2. Basic setting requirements for wave soldering:
(1) Tin immersion time: crest 1 is controlled in 0.3~1 seconds, and crest 2 is controlled in 2~3 seconds;
(2) Conveying speed: 0.8~1.5 m/min;
(3) The pinch inclination angle is 4-6 degrees;
(4) The flux spray pressure is 2-3Psi;
(5) The pressure of the needle valve is 2-4Psi;
3. After the plug-in material is passed through wave soldering, the product needs to be fully inspected and separated from the board with foam to avoid collision and rubbing.
SMT patch test
1. ICT test, the defective board and the qualified product are placed separately, and the board that passes the test needs to be labeled with ICT test label and separated from foam.
2. FCT test, the defective board and the qualified product are placed separately, and the qualified board needs to be labeled with FCT test label and separated from the foam. A test report needs to be made, and the serial number on the report should correspond to the serial number on the PCB board, and the defective board will be sent for repair and the defective product repair report will be done.
Pack
1. For process operation, use turnover cart or anti-static thick foam turnover, PCBA can not be stacked, avoid collision, and top pressure;
2. Paste PCBA shipment, use anti-static bubble bag packaging (the size of the electrostatic bubble bag must be the same), and then use foam packaging to prevent external force to reduce buffering, foam more than 5cm PCBA, and use adhesive tape to fix the packaging, use electrostatic rubber box for shipment, and increase the partition in the middle of the product.
3. The glue box can not be pressed to the PCBA, the inside of the glue box is clean, and the outer box is clearly marked, including the content: processing manufacturer, instruction number, product name, quantity, and delivery date.
Maintenance
1. Do a good job of report statistics for each section of maintenance products, model, defective type, and defective quantity;
2. Repair refer to IPQC to confirm the replacement of sealing samples and repair components;
3. The maintenance product is required not to burn, damage the surrounding components, PCB copper foil, after the maintenance of the product using alcohol to clean the surrounding foreign bodies, the maintenance staff to do a good job of re-inspection, and in the blank area of the barcode paste with a pen to hit "." Distinguish;
4. After SMT repair, the product needs to be fully tested by AOI, and the product needs to be fully tested by function after power test maintenance;
5. Mantissa products, maintenance, and patch board products must be arranged for testing, and it is strictly forbidden to ship directly without testing.
Shipment
FCT test report, defective product maintenance report, and shipment inspection report are indispensable when shipping.
Exception handling
1. The material abnormality will be confirmed and handled by the processing plant by email and telephone feedback to our company;
2. At the process end of the processing plant, the defective rate of more than 3% needs to be reviewed and improved;
3. The shipped products need to ensure product quality, and the abnormal feedback is confirmed and processed within 2H-4H, and the defective products are isolated and re-inspected, and the same problems are fed back for 2 consecutive times without improvement, and we will give punishment to the relevant departments and workers.