What is SMT assembly?
Surface Mount Technology (SMT) is an electronic assembly method where electronic components are directly mounted onto the surface of a printed circuit board (PCB) without the need for traditional through-hole techniques. Compared to through-hole technology, SMT simplifies the production process, reduces the need for drilling and complex lead usage, and enables the manufacturing of smaller, more compact electronic devices.
SMT Assembly Process
SMT assembly is characterized by high levels of automation, enabling the rapid and precise placement of components on PCBs. This process involves several key steps:
Solder Paste Application:
Solder pads are prepared with solder paste, typically applied using a stencil process that resembles silk-screen printing. The stencil ensures precise application of solder to the areas where surface-mount devices (SMDs) will be placed. The solder paste acts as both an adhesive and a conductor, allowing components to bond securely to the board.
Automated Component Placement:
Once the solder paste is applied, highly specialized machines pick and place components onto the board with extreme accuracy. Components are fed to the machine via reels or trays, and the machine aligns and positions each component on the corresponding solder pads. This level of automation eliminates manual placement, reducing human error and increasing production speed.
Reflow Soldering:
The next step is reflow soldering, where the entire board is heated to melt the solder paste, creating a permanent bond between the components and the PCB. Reflow ovens are used to achieve this, and several methods can be employed, including:
- Infrared Reflow: This method uses infrared radiation to heat the solder.
- Convection Reflow: Hot air circulates within the oven to transfer heat evenly.
- Vapor Phase Reflow: A vaporized liquid transfers heat to the solder, providing precise temperature control.
Each method has advantages and drawbacks, particularly when considering environmental concerns such as lead-free soldering, which requires higher temperatures.
Double-Sided Assembly:
If the PCB design requires components on both sides, the process is repeated for the opposite side. Care must be taken to ensure components on the first side are not damaged during the second round of heating. Heat-sensitive components may be added later to avoid exposure to the reflow process.
Cleaning and Residue Removal:
After soldering, PCBs often contain flux or solder residues that can cause short circuits if not removed. Cleaning processes are used to wash away excess materials, leaving the boards free of contamination.
Inspection and Testing:
SMT assembly involves rigorous inspection and testing to ensure quality. Automated Optical Inspection (AOI) systems compare the final product to a reference image to detect issues such as misaligned components, insufficient solder, or missing parts. Additionally, functional testing verifies that the circuit performs as expected before shipping.
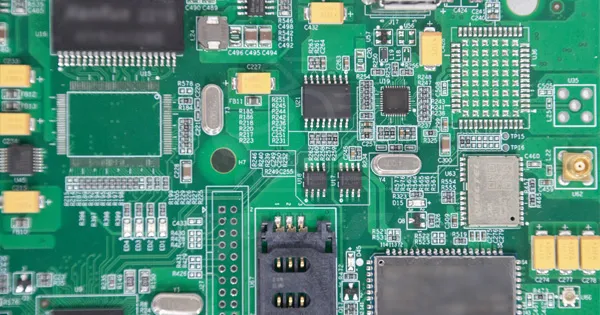
SMT Assembly Benefits in PCBA Manufacturing
Surface Mount Technology (SMT) offers several notable advantages in
PCBA manufacturing, particularly when it comes to efficiency, cost reduction, and design flexibility in mass production. Here’s an outline of these advantages:
Cost Reduction
SMT significantly lowers production costs by simplifying the manufacturing process. Traditional through-hole technology requires drilling and inserting component leads, which is both time-consuming and increases manufacturing costs. SMT eliminates most of the drilling requirements, making the process more efficient. Additionally, SMT components are smaller and lighter, which reduces the consumption of raw materials, leading to further cost savings.
Smaller, Lighter Devices
SMT allows components to be mounted on both sides of the PCB, greatly increasing component density and design flexibility. The small size of SMT components enables more compact PCBA designs, which is crucial for industries such as smartphones, tablets, wearable devices, and aerospace, where miniaturization and high efficiency are essential.
Automation and Consistency
The SMT assembly process is highly automated, using machinery to accurately place and solder components. Modern SMT equipment can place tens of thousands of components per hour with high precision, speeding up production and reducing errors and defects. This automation enhances consistency in production, ensuring quality and stability in large-scale manufacturing.
Improved Electrical Performance
SMT components are typically smaller and have shorter leads, reducing resistance and inductance in the circuit, which improves signal transmission and overall electrical performance. This advantage is especially important for high-frequency applications, such as 5G communications, data centers, and high-performance computing devices.
Enhanced Design Flexibility
SMT eliminates the need for through-holes, allowing designers to mount components on both sides of the PCB. This offers greater freedom in design, making circuits more compact and efficient, and enabling the integration of more advanced features, particularly in space-constrained devices. Additionally, SMT components can coexist with through-hole components, accommodating designs that require higher mechanical strength or thermal management.
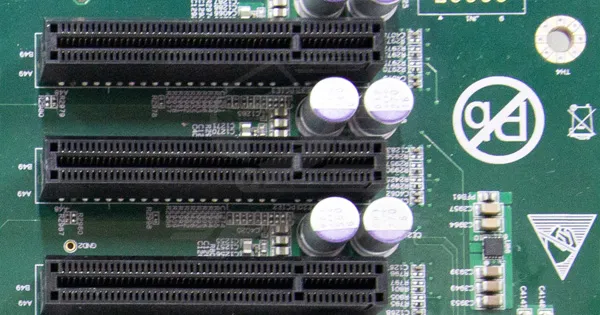
Scalability for Mass Production
SMT’s high level of automation makes it highly scalable, allowing PCBA manufacturers to increase output without compromising quality. This scalability is crucial for industries like consumer electronics and automotive manufacturing, where millions of units may be produced annually. SMT provides an efficient solution for large-scale operations with minimal defect rates.
Assembly Speed and Reduced Manual Intervention
SMT reduces the need for manual intervention compared to traditional through-hole technology. Through-hole techniques require workers to manually align component leads and insert them into drilled holes, whereas SMT relies on automated machines to place components, significantly increasing production speed and reducing human error. Automated equipment can place over 25,000 components per hour, further enhancing efficiency.
Component Density and Double-Sided Assembly in SMT
SMT allows for more components to be placed within the same space, increasing component density and enabling modern electronic devices to be more functional while maintaining a smaller footprint. Double-sided assembly is another key advantage of SMT, allowing components to be mounted on both sides of the PCB, maximizing space utilization and enabling more complex designs. This flexibility is especially beneficial for size-sensitive devices, such as smartphones and wearable technology.
Coexistence with Through-Hole Components
While SMT has become the standard for most PCB assemblies, certain applications still require through-hole components, especially in cases where additional mechanical strength is needed, such as power connectors and heat sinks. SMT and through-hole components can coexist on the same board, providing designers with more options and balancing reliability and flexibility.
SMT’s Key Role in Modern Electronics
SMT assembly has revolutionized the PCBA manufacturing process, offering benefits beyond cost savings and automation. By eliminating the need for drilling, reducing manual intervention, and increasing production speed and flexibility, SMT has become the backbone of modern electronics manufacturing. The ability to produce smaller, lighter, and more complex circuit boards has made SMT an indispensable technology for the future of electronics.
With advantages like enhanced reliability, improved performance, and scalability for mass production, SMT has become the preferred method for manufacturers worldwide. As the demand for compact, high-performance electronic devices continues to grow, SMT will remain a driving force behind advancements in consumer electronics, aerospace, automotive, and telecommunications sectors.