In the circuit board manufacturing industry, a series of quality standards and certification systems are widely applied to ensure product quality, improve management efficiency, and meet the requirements of specific industries or markets. These standards cover various aspects of the quality management system, as well as special requirements for certain industries or products. In this article, we will focus on 5 important standards: IATF16949, UL, IPC, ISO9001, and RoHS. SprintPCB has obtained the following Key
PCB Certifications:
1. What is IATF 16949 Certification?
IATF 16949 is an internationally recognized quality management system standard for the automotive industry, developed by the International Automotive Task Force (IATF). The core goal of this standard is to align global quality management systems across the automotive supply chain, improve product quality, prevent defects, reduce quality fluctuations, and eliminate waste in the supply chain, ultimately enhancing production efficiency.
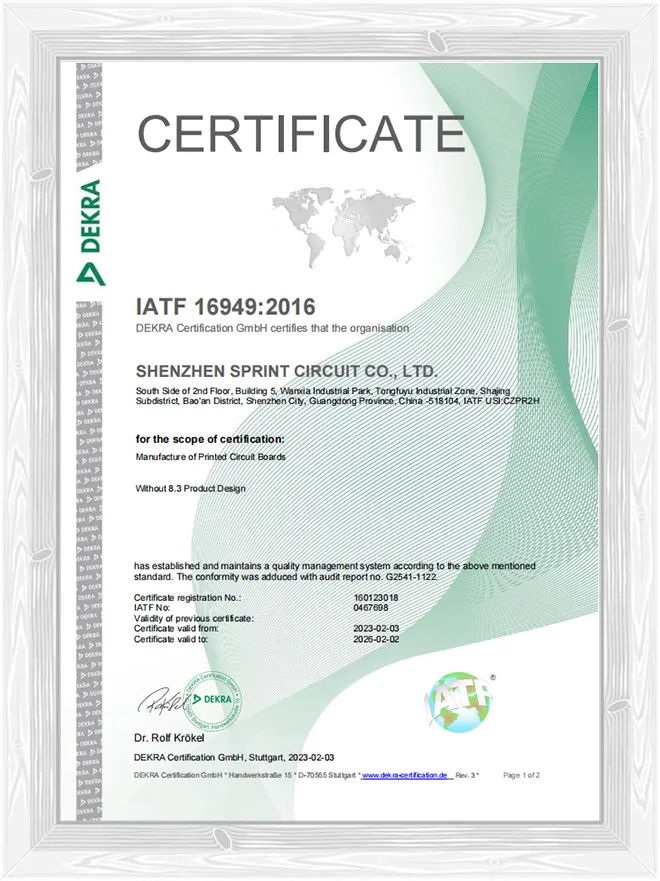
Scope of IATF 16949
IATF 16949 is specifically designed for the automotive industry and is especially relevant to manufacturers of critical automotive PCB systems, such as engine control, chassis control, body electronics, and safety systems. For
automotive PCB manufacturers, achieving IATF 16949 certification is crucial to ensuring that their PCB products meet the stringent quality and reliability requirements of the automotive industry.
This certification not only acknowledges product quality but also affirms the management level of the company. Achieving the certification helps build customer trust and enhance market competitiveness. For SprintPCB, obtaining IATF 16949 certification signifies that its product quality is recognized, and its management capabilities and technical expertise are elevated.
Advantages of IATF 16949
Enhanced Quality Management: Systematic quality management methods reduce defects and improve product consistency and reliability.
Cost Reduction: Preventive measures and continuous improvement help lower quality costs and production losses.
Improved Customer Satisfaction: Higher product quality and reliability increase customer satisfaction and trust.
By implementing these key requirements, companies can ensure their products meet standards, improve production efficiency, reduce costs, and enhance competitiveness in the market.
2. ISO9001 Quality Management
ISO 9001 is a widely recognized quality management system standard, providing PCB manufacturers with a systematic approach to managing quality. It ensures that products meet customer requirements and regulatory standards, improving overall operational efficiency and market competitiveness.
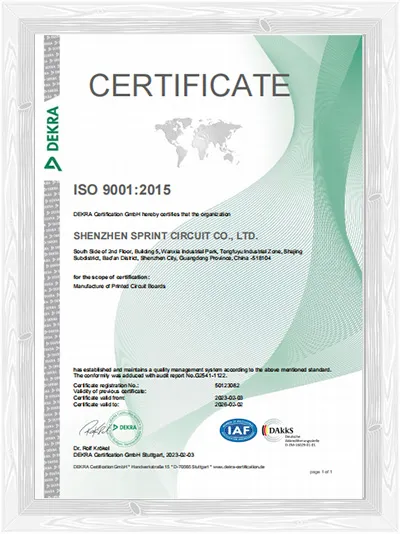
Scope of ISO 9001 in PCB Manufacturing
Production Process Management:
PCB manufacturing involves various complex production stages, such as material procurement, design, etching, drilling, soldering, and testing. ISO 9001 requires companies to establish clear process specifications and execution standards to ensure each stage meets predefined quality standards, optimizing internal management and reducing waste.
Quality Control:
By implementing ISO 9001 standards, PCB manufacturers can establish and improve quality control processes using ISO 9001’s tools and methods, such as statistical process control (SPC) and quality function deployment (QFD), to monitor and improve production processes, ensuring product stability and reliability.
Supply Chain Management:
PCB manufacturing requires the procurement of raw materials and components, as well as outsourcing certain processes. ISO 9001 requires companies to establish a robust supply chain management system, ensuring that suppliers provide qualified materials and components, while regular evaluations maintain the stability and reliability of the supply chain.
Risk Management:
PCB manufacturing involves several potential risk factors, such as equipment failure, material defects, and human error. ISO 9001 emphasizes identifying, assessing, and controlling these risks to minimize rework and waste, ensuring production stability and reliability.
By implementing the ISO 9001 quality management system certification, PCB manufacturers can optimize internal management, enhance product quality, and strengthen supply chain and risk management capabilities. SprintPCB’s ISO 9001 certification reflects a significant improvement in its product quality, management level, and market competitiveness.
3.What is UL Certification?
UL (Underwriters Laboratories) is an independent, global safety science company dedicated to setting and certifying safety standards for public and product safety. In the circuit board manufacturing industry,
UL standards and certifications play a crucial role in ensuring the safety, reliability, and compliance of products. UL has established several stringent standards for PCBs, such as UL 94 (flammability testing for plastic materials) and UL 796 (standards for printed circuit boards), covering aspects like material selection, manufacturing processes, performance testing, and quality control.
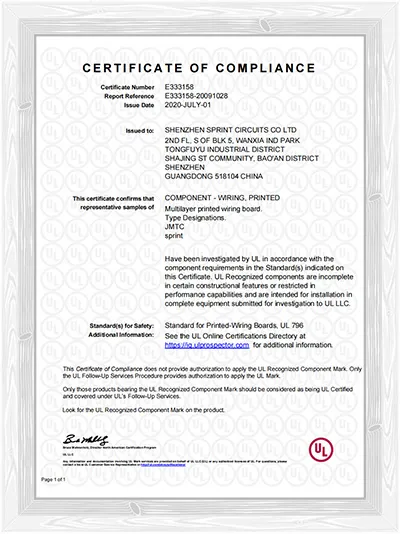
A PCB certified by UL not only demonstrates compliance with international safety standards but also enhances its market competitiveness and customer trust, helping manufacturers expand their market reach and secure more business opportunities. Its key roles include ensuring electrical safety, mechanical performance, and fire resistance of products; helping companies meet legal and industry standards, thereby reducing legal risks.
Key UL Certification Requirements for PCB Manufacturing:
Material Requirements
Base Material Certification (UL 94): PCB base materials like FR-4 and CEM-1 need to pass UL 94 flammability tests, which assess how materials behave when exposed to flame or high temperatures. These materials are rated into categories such as HB, V-0, V-1, and V-2, ensuring sufficient fire-resistant properties.
Copper-Clad Laminate Certification: The electrical performance, mechanical strength, and fire resistance of copper-clad laminates must also meet UL certification to ensure their safety.
Manufacturing Process Requirements
Lamination Process: UL enforces strict requirements for the lamination process to ensure stable bonding under high temperature and pressure, preventing delamination or blistering.
Plated-Through Hole (PTH) Process: The PTH process must meet UL standards, ensuring good adhesion of the plating layer and electrical conductivity, which guarantees the electrical performance and long-term reliability of the PCB.
Finished Product Testing
Electrical Performance Testing: UL certification requires PCB manufacturers to conduct tests such as dielectric strength, insulation resistance, and conductivity to ensure electrical safety under various operating conditions.
Mechanical Performance Testing: This includes tests for bending strength, impact strength, and peel strength to ensure the PCB’s stability and durability under mechanical stress.
Fire Performance Requirements
UL 94 Flammability Test: This test evaluates how PCB materials behave under direct flame or high temperatures. Certified materials are categorized by factors like burn rate and dripping behavior into classifications such as HB, V-0, V-1, and V-2, ensuring fire-resistant performance.
Fire-Retardant Additives: Flame-retardant additives used to enhance PCB fire resistance must pass UL certification, ensuring they do not compromise the electrical or mechanical performance of the PCB.
Manufacturing Process Control Requirements
Production Process Monitoring: PCB manufacturers must establish stringent process control systems, including monitoring and recording key process parameters, to ensure that each production step complies with UL standards.
Quality Management System: Manufacturers are required to implement a comprehensive quality management system, covering the entire process from raw material procurement, production, and testing to final product delivery, ensuring traceability.
Reliability and Durability Requirements
Thermal Aging Test: This test evaluates the long-term stability and performance of the PCB in high-temperature environments, ensuring its reliability under harsh conditions.
Humidity Test: Tests the PCB's performance in high-humidity environments, including moisture absorption and conductivity changes, ensuring reliability in damp conditions.
SprintPCB’s UL certification not only proves that its products meet international safety standards but also increases market recognition, competitiveness, and customer trust.
4.What is IPC Standards PCB?
IPC standards, developed by the Institute for Interconnecting and Packaging Electronic Circuits, are a comprehensive set of regulations that cover every phase of electronic product design, manufacturing, assembly, and testing. Founded in 1957, IPC initially focused on printed circuit boards (PCBs) but has since grown into a global authority in the electronics industry.
These standards, created and updated by global experts and industry representatives, are widely regarded as the "quality guidelines" of the electronics sector, ensuring product quality and consistency.
The Role of IPC Standards
IPC standards are primarily used to ensure the quality and consistency of electronic products. As the complexity of electronic product design and manufacturing increases, IPC standards provide engineers, designers, and manufacturers with a unified reference framework. This standardization not only streamlines production but also improves product reliability and minimizes potential quality issues.
Quality Assurance and Product Reliability
One of the major advantages of IPC standards is their ability to ensure product quality. For example, IPC-A-600 outlines the acceptability criteria for printed circuit boards, and manufacturers that adhere to these guidelines can guarantee the quality of their products.
Improved Communication and Collaboration
IPC standards provide a unified language for the industry, enabling efficient communication across design, manufacturing, and procurement teams, avoiding misunderstandings caused by inconsistent terminology.
Process Optimization
Every stage of production is tested and controlled according to IPC standards. Workers and managers are trained based on these standards, ensuring high efficiency and consistency in the production process.
Cost Savings
By adhering to IPC standards, manufacturers can reduce production errors and trial-and-error costs. The standardized processes and material requirements help companies lower research and development costs and improve overall efficiency.
Enhanced Brand Reputation
Products manufactured to IPC standards are reliable, boosting customer confidence and opening more market opportunities. Suppliers who produce according to IPC standards are more likely to win customers because their products are perceived as more dependable and of higher quality.
Through understanding and implementing IPC standards, SprintPCB achieves efficient production, cost savings, and enhanced market competitiveness.
IPC Classification Levels
IPC Class 1 Standards: General electronic products, such as flashlights, toys, and remote controls, use PCBs that do not require high-quality standards and have relatively short lifespans.
IPC Class 2 Standards: This class includes electronics with longer lifespans, like microwaves, smartphones, and laptops, with performance and durability prioritized.
IPC Class 3 Standards: High-reliability electronics, such as medical devices and aerospace equipment, require the highest levels of precision and quality.
5.What is RoHS?
What is RoHS?
RoHS, which stands for "Restriction of Hazardous Substances," is an environmental regulation designed to limit the use of hazardous materials in electrical and electronic products. Its goal is to minimize potential harm to human health and the environment.
What is the purpose of RoHS certification?
The primary objective of RoHS is to encourage companies to adopt more environmentally friendly materials and production processes, reducing the potential environmental and health risks posed by electronic products. By restricting the use of certain hazardous substances, RoHS promotes sustainability and increases environmental awareness within the electronics industry. For companies aiming to enter the European market, compliance with RoHS certification is mandatory, ensuring that their products meet EU environmental regulations.
Restricted Substances and Scope of RoHS
RoHS limits the use of the following 10 hazardous substances:
- Lead (Pb): Commonly found in solder, glass, and PVC stabilizers.
- Mercury (Hg): Used in thermostats, sensors, switches, relays, and light bulbs.
- Cadmium (Cd): Found in switches, springs, connectors, PCBs, contacts, and batteries.
- Hexavalent Chromium (CrVI): Used in corrosion protection coatings on metals.
- Polybrominated Biphenyls (PBBs): Flame retardants used in PCBs, connectors, and plastic housings.
- Polybrominated Diphenyl Ethers (PBDEs): Another flame retardant used in PCBs and plastic housings.
- Diethylhexyl Phthalate (DEHP): A plasticizer used in plastics.
- Benzyl Butyl Phthalate (BBP): Found in flexible plastics.
- Dibutyl Phthalate (DBP): Used in flexible plastic products.
- Diisobutyl Phthalate (DIBP): Another plasticizer used in plastic products.
RoHS not only applies to a wide range of electronic and electrical products but also affects the entire production chain, including components, raw materials, and packaging. Below is a detailed breakdown of the industries covered by the RoHS directive:
The scope of the RoHS directive includes household appliances (e.g., refrigerators and washing machines), small appliances (e.g., vacuum cleaners and irons), IT and communication equipment (e.g., computers and mobile phones), consumer devices (e.g., televisions and radios), lighting equipment (e.g., fluorescent lamps), power tools (e.g., drills and lathes), toys and entertainment devices (e.g., video game consoles), medical devices (e.g., electrocardiograms), monitoring and control instruments (e.g., smoke detectors), and vending machines.
RoHS also applies to automotive electronics, home medical devices, smart home products, portable electronic devices, batteries, energy storage systems, communication infrastructure equipment, and industrial devices. These products and their components must comply with RoHS standards to reduce the use of harmful substances and promote environmental sustainability.
The importance of PCB certification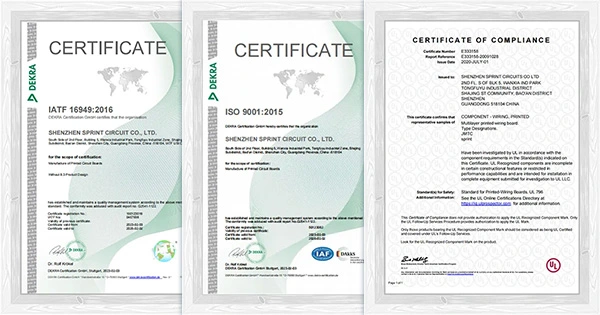
Adhering to international and regional standards is crucial for ensuring product quality, compliance, and market competitiveness in the global electronics industry. IPC standards provide consistent guidelines for the design and manufacturing process, improving the reliability and efficiency of electronic products. UL certification ensures products meet safety requirements and enhances market acceptance. The RoHS directive limits the use of hazardous substances, fostering environmental protection and sustainability. IATF and ISO standards further enhance the global consistency of manufacturing processes and quality management.
SprintPCB has already achieved these certifications and standards. For more information or inquiries, feel free to
contact us anytime.