In modern electronic device design and manufacturing, selecting the appropriate type of circuit board is crucial. Rigid-flex boards and flexible printed circuit boards (FPC) are two common options that play important roles in different application scenarios.
Rigid-flex boards are designed to combine the characteristics of both rigidity and flexibility, providing flexibility and bending capabilities in certain areas while maintaining rigidity in others. On the other hand, FPCs are renowned for their bending and pliability, making them suitable for applications that require miniaturization and high-density wiring.
Choosing the right circuit board type for a specific project is essential to ensure the performance, reliability, and production efficiency of electronic devices. However, for many designers and manufacturers, the decision between rigid-flex board and FPC can be challenging.
Therefore, this article aims to explore the advantages and disadvantages of rigid-flex boards and FPCs and provide key considerations to help readers make informed decisions regarding the trade-offs.
By understanding the characteristics and applications of rigid-flex boards and FPCs, readers will be able to make wise decisions based on the requirements and constraints of their projects. Whether it is pursuing higher space efficiency and design flexibility or focusing on cost and production efficiency improvements, this article will provide comprehensive information to assist readers in making informed choices between rigid-flex boards and FPCs.
Next, we will delve further into the article to discuss
the advantages and disadvantages of rigid-flex board and FPC, as well as the key considerations for selection.
Advantages of Rigid-flex board
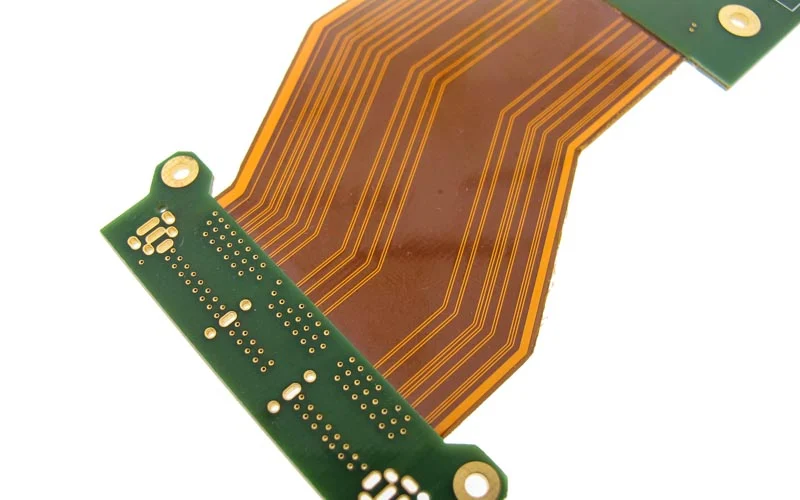
Rigid-flex boards offer the functionality of both rigid and flexible parts on a single circuit board. This design reduces the number of interconnections and connectors between components, saving space and making it easier to integrate electronic elements into compact devices or systems. Additionally, the design flexibility of rigid-flex boards allows for customized layouts to better suit specific application requirements, accommodating complex electronic designs.
The combination of rigid and flexible materials in rigid-flex boards provides higher reliability and durability. The rigid portion provides stable support and mechanical strength, preventing the board from being damaged during vibration or bending. The flexible portion can adapt to bending and twisting, reducing mechanical stress, thereby improving the board's lifespan and reliability.
The design of rigid-flex boards eliminates the need for a large number of connectors and plugins required in traditional circuit boards. This reduces the number of connection points, minimizing potential connection issues and failure points, thereby improving the overall circuit reliability. Furthermore, reducing the number of connectors simplifies the assembly process, saving production costs and time.
The design of rigid-flex boards can reduce the number of components and assembly steps, leading to lower manufacturing costs and assembly time. Compared to traditional methods that involve using separate circuit boards and wire harnesses, the integrated design of rigid-flex boards reduces errors and failures during assembly, improving production efficiency.
Disadvantages of Rigid-flex board
The design of rigid-flex board is complex as it requires the integration and routing of two different materials. This may necessitate advanced design skills and tools. Additionally, the manufacturing cost of rigid-flex boards is typically higher compared to traditional rigid or flexible circuit boards. This includes material costs, processing techniques, and specialized production equipment.
The manufacturing and assembly processes of rigid-flex boards are more intricate than those of traditional circuit boards. Due to the unique structure, special manufacturing techniques and equipment are required to ensure the reliability and stability of the flexible parts. Furthermore, assembling rigid-flex boards demands higher technical expertise and meticulous handling to properly combine and secure the connection points between the rigid and flexible sections.
The complexity of the structure in rigid-flex boards makes repair and restoration more challenging. Repairing the flexible portion may necessitate specialized techniques and equipment, while fixing the rigid portion may require redesigning and remanufacturing the entire circuit board. Therefore, the cost and time investment for maintaining and repairing rigid-flex boards are high.
The design and manufacturing of rigid-flex board are suitable for specific application scenarios. For certain requirements such as high-temperature environments, high current conduction, or mechanical stress, rigid-flex board may not be the most suitable choice. This is because the flexible parts may become unstable or susceptible to damage under certain extreme conditions. Hence, when selecting rigid-flex boards, careful consideration of the specific demands and limitations of the application is necessary.
Advantages of FPC
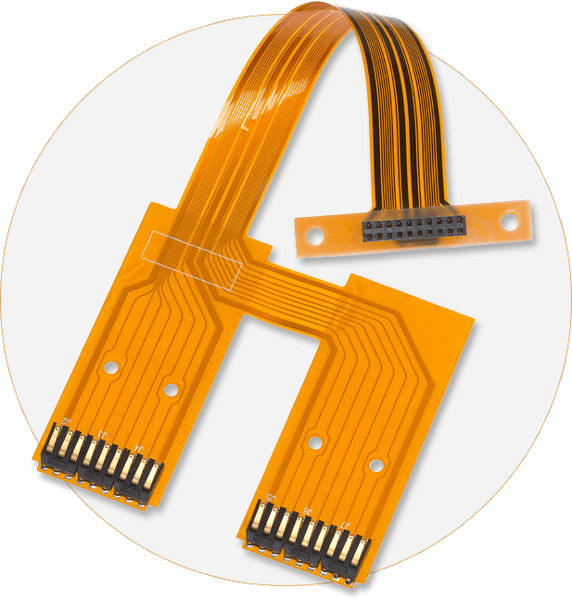
Flexible circuit boards can bend and fold, making them adaptable to various shapes and sizes of devices. This flexibility makes flexible circuit boards particularly suitable for applications with limited space or requiring curved installations.
Flexible circuit boards are made of thin and lightweight flexible substrates, making them thinner and lighter compared to rigid circuit boards. This makes flexible circuit boards very useful in small devices with restrictions on weight and volume, such as mobile devices, wearable devices, and medical equipment.
Flexible circuit boards enable high-density wiring as they can accommodate more circuits by using thin films, multilayer stacking, or curved paths. This provides more connection points and higher wiring density, facilitating the design of complex circuits and functionalities. Additionally, flexible circuit boards reduce the number of connection points and connectors, thereby reducing potential failure points and improving system reliability.
The flexible substrates of flexible circuit boards typically exhibit good electromagnetic shielding performance. They can offer lower electromagnetic radiation and sensitivity, thereby reducing the impact of interference and noise. This is crucial for high-frequency and sensitive applications such as communication devices and RF circuits.
Flexible circuit boards typically employ reliable connection methods like soldering or compression bonding to connect electronic components and devices. These connection methods provide good electrical connections and mechanical fixation, capable of withstanding environmental stresses like vibrations, shocks, and temperature changes.
The flexible substrates and reliable connection methods of flexible circuit boards make them possess good resistance to vibration and shock. They can maintain circuit stability and reliability in vibrating and impacting environments, making them suitable for applications such as mobile devices and automotive electronics that are sensitive to vibrations and shocks.
Disadvantages of FPC
Flexible circuit boards are more susceptible to mechanical stress compared to rigid circuit boards. Due to their thin and flexible nature, flexible circuit boards are prone to bending, folding, or being damaged under improper handling. Therefore, they require careful handling and maintenance in applications to ensure their mechanical strength and durability.
In comparison to rigid circuit boards, flexible circuit boards have higher manufacturing costs. The manufacturing process of flexible circuit boards involves special materials and techniques such as polyimide (PI) substrate materials, thin-film plating, lamination, and so on. These special requirements make the manufacturing process more complex, requiring higher technological expertise and equipment investment, thus increasing the cost.
Flexible circuit boards are more sensitive to environmental conditions. For example, they are more sensitive to temperature variations, humidity, and chemical substances. In harsh environmental conditions such as high temperatures, high humidity, corrosive gases, flexible circuit boards may be affected, leading to performance degradation or failure. Therefore, the use of flexible circuit boards may be limited in certain specific application environments.
Flexible circuit boards have certain limitations in high-frequency and high-speed applications. Due to their flexible substrate and thin conductors, the electrical transmission characteristics of flexible circuit boards may be affected by losses and signal attenuation, limiting their ability in high-frequency and high-speed signal transmission. For applications requiring higher frequencies or fast signal transmission, more complex designs and technological solutions may be required.
In comparison to rigid circuit boards, the design and maintenance of flexible circuit boards are relatively more complex. Due to the flexibility and softness of flexible circuit boards, the design process needs to consider additional factors such as folding points, bending radii, and the use of connectors. Additionally, repairing and maintaining flexible circuit boards can be more challenging due to their flexibility and complex structure, often requiring specialized expertise and equipment.
SprintPCB: Your Reliable PCB Support Provider
SprintPCB is a renowned high-tech enterprise offering comprehensive PCB manufacturing services to clients globally. With our extensive expertise and cost-effective solutions, you can prioritize your organization's critical requirements while enjoying a seamless process. Get in touch with us today and discover how we can assist you.