In the world of electronics, printed circuit boards (PCBs) play a crucial role in providing a platform for interconnecting electronic components. Over the years, technological advancements have led to the development of various types of PCBs, including Metal Core PCBs. In this article, we will delve into the world of Metal Core PCBs, understanding their definition, types, advantages, and applications.
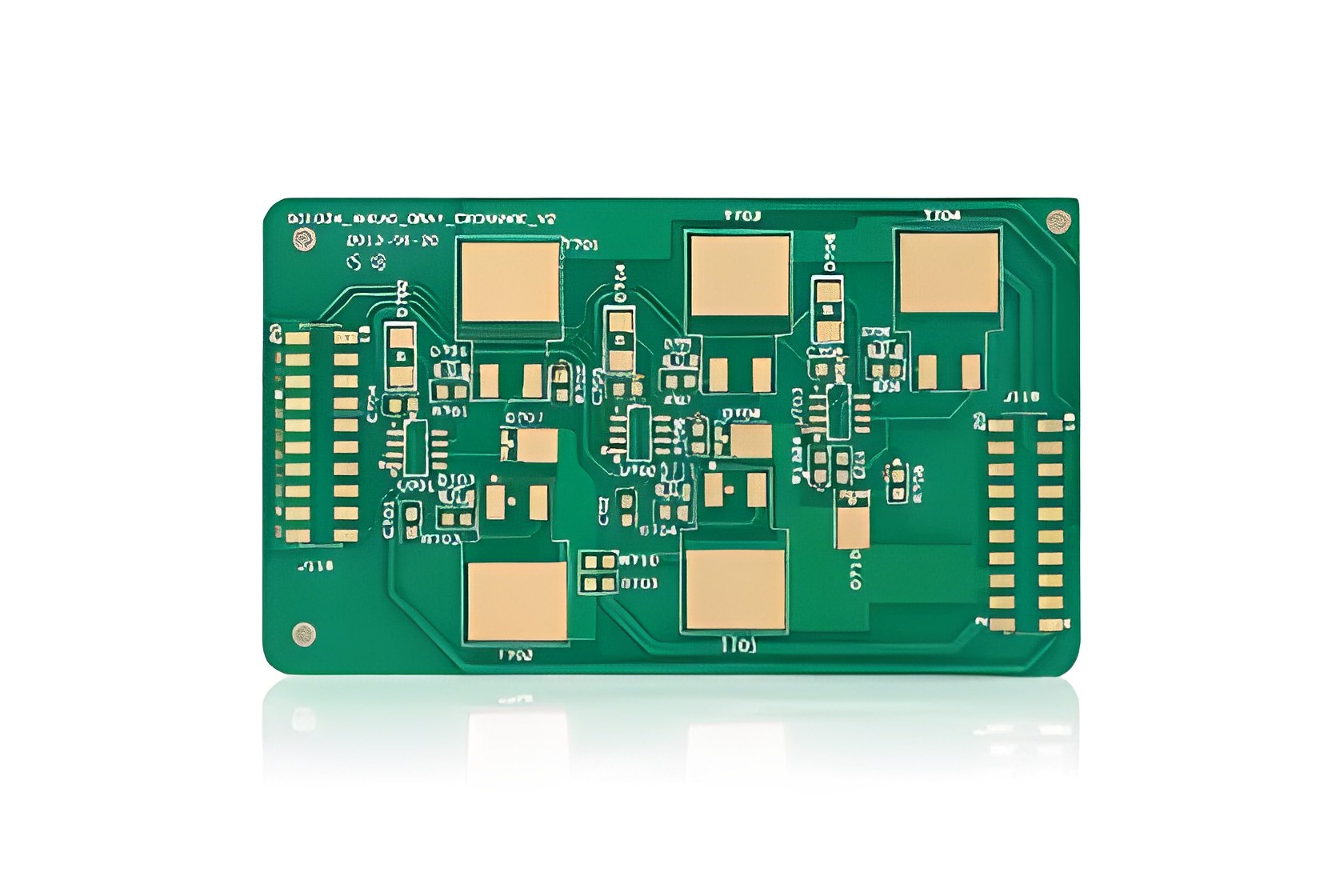
The definition and construction of Metal Core PCB:
Metal Core PCBs, also known as Metal Core PCBs (MCPCBs), are a specialized type of PCB that incorporates a metal base layer in its construction. Unlike traditional PCBs that use rigid or flexible substrates made of materials like FR-4 or polyimide, Metal Core PCBs utilize metals such as aluminum or copper as the core material. The metal base layer provides improved thermal conductivity and enhanced mechanical strength.
The differences between Metal Core PCB and traditional FR-4 PCB (based on glass fiber-reinforced epoxy resin)
Material composition: Metal Core PCB utilizes a metal substrate, typically aluminum or copper, whereas FR-4 PCB uses glass fiber and resin materials. This material difference directly affects the performance and characteristics of the PCB.
Thermal management capability: Metal Core PCB excels in thermal conductivity due to its metal substrate, enabling effective heat dissipation. This provides an advantage in high-power and heat-sensitive applications. In contrast, FR-4 PCB has weaker thermal management capability and may require additional heat dissipation solutions.
Electrical properties: The metal substrate of Metal Core PCB exhibits good electrical conductivity, reducing impedance and noise interference in signal transmission. In comparison, FR-4 PCB has lower conductivity, potentially necessitating more complex layer design and signal integrity measures to ensure electrical performance.
Mechanical strength: Thanks to the advantages of the metal substrate, Metal Core PCB typically possesses higher mechanical strength and shock resistance, better withstanding vibrations and impacts. FR-4 PCB, on the other hand, is fragile and may require additional mechanical protection measures in certain application environments.
Manufacturing complexity: Due to the unique nature of the metal substrate, the manufacturing process of Metal Core PCB is complex, requiring special processes and equipment to handle the bonding and processing of metal with other layers. In contrast, FR-4 PCB follows established standard manufacturing processes, resulting in lower manufacturing complexity.
The types of Metal Core PCB:
Metal Core PCBs are a special type of printed circuit boards that offer unique performance and advantages by incorporating a metal base layer in their construction. Here are some common types of Metal Core PCBs:
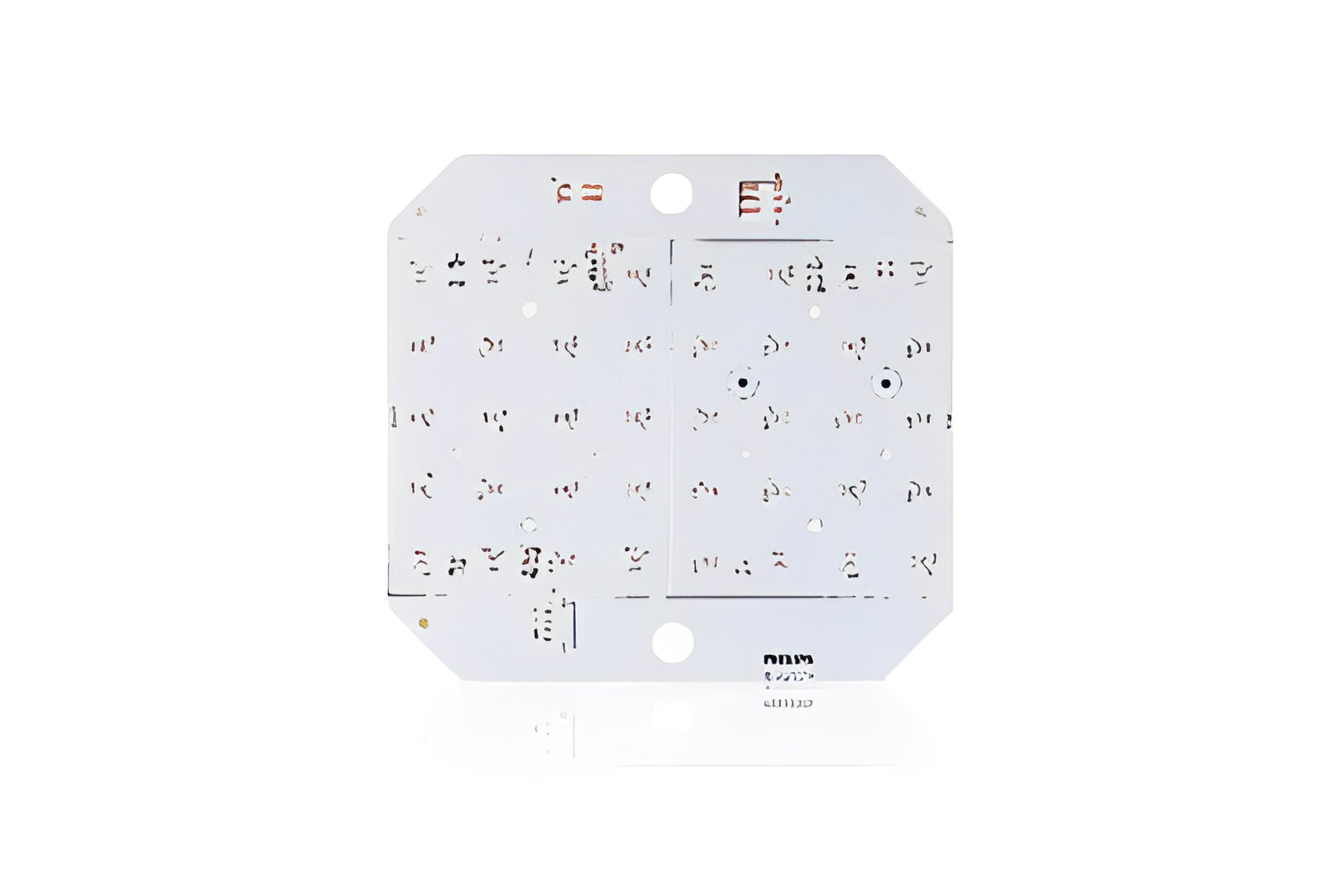
Aluminum-based PCBs:
Aluminum-based PCBs are the most common and widely used type of Metal Core PCBs. They use aluminum as the base material, providing excellent thermal conductivity and mechanical strength. Aluminum-based PCBs are typically suitable for general power applications, LED lighting, and electronic heat sinks.
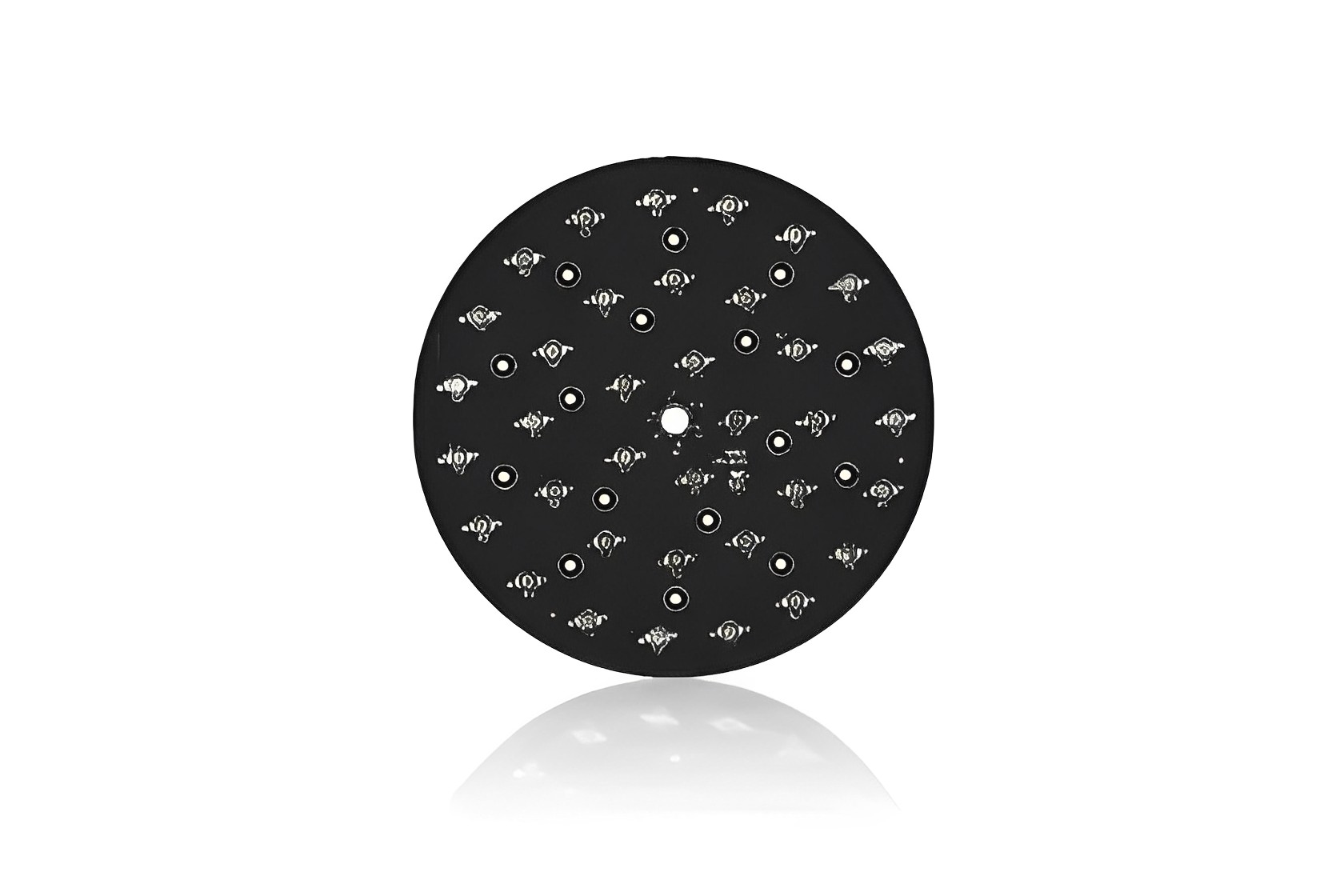
Copper-based PCBs:
Copper-based PCBs are another common type of Metal Core PCBs. Compared to aluminum-based PCBs, copper-based PCBs have higher thermal and electrical conductivity, making them more suitable for high-power applications and high-frequency circuits. Copper-based PCBs are commonly used in power amplifiers, high-speed communication equipment, and radio frequency electronic devices.
Iron-based PCBs:
Iron-based PCBs are less commonly used but still have specific applications. Iron-based PCBs have higher magnetic permeability, making them suitable for magnetic components and magnetic sensors in specialized applications.
Nickel-based PCBs:
Nickel-based PCBs offer good corrosion resistance and high-temperature stability, making them popular for applications with special environmental requirements. They are commonly used in aerospace, military, and high-temperature electronic devices.
Alloy-based PCBs:
Alloy-based PCBs are a type of Metal Core PCB that combines different metals. By adjusting the composition of the alloy, specific performance requirements can be achieved. Alloy-based PCBs are used in specialized applications such as high-power density electronic devices and electronic components in special environments.
It is important to note that different types of Metal Core PCBs are suitable for different applications and environments. The choice of the appropriate type depends on specific project requirements, such as power demands, thermal management needs, and electromagnetic compatibility. Design engineers typically select the most suitable type of Metal Core PCB based on the project's requirements and constraints to ensure optimal performance and reliability.
One of the primary advantages of Metal Core PCBs is their excellent thermal management capability. The metal core allows for efficient dissipation of heat generated by power components, preventing overheating and improving overall system reliability.
Metal Core PCBs are well-suited for high power applications due to their superior thermal conductivity. They can handle higher currents and dissipate heat more effectively, making them ideal for power electronic devices, LED lighting systems, and automotive applications.
Metal Core PCBs offer a lightweight and compact solution for electronic assemblies. The use of metal cores allows for the reduction of board thickness while maintaining structural integrity, enabling designers to create more compact and space-saving products.
Metal Core PCBs exhibit excellent mechanical strength and durability, making them resistant to warping and cracking. This ensures the reliability and longevity of electronic devices even under harsh operating conditions.
Applications of Metal Core PCB:
LED Lighting:
Metal Core PCBs are widely used in the LED lighting industry. Due to the significant heat generated during the operation of LED fixtures, the excellent thermal conductivity of Metal Core PCBs makes them an ideal choice. Metal Core PCBs efficiently transfer heat from the LED chips to the heat sink, providing effective heat dissipation, thereby extending the lifespan of LED fixtures, and improving their performance and reliability.
Automotive Electronics:
In the field of automotive electronics, Metal Core PCBs find extensive applications in vehicle lights, onboard electronic control modules, and electric vehicles. The harsh conditions of the automotive environment, including high temperatures and vibrations, demand superior thermal management and mechanical strength, which Metal Core PCBs offer. This ensures the stability and reliability of electronic devices in automobiles.
Communication Equipment:
Metal Core PCBs play a crucial role in communication equipment. They are utilized in base stations, radio frequency modules, network switches, and other high-power and high-frequency applications. Metal Core PCBs efficiently dissipate heat, provide stable signal transmission, and deliver better performance, meeting the requirements of high-density and compact designs in communication devices.
Solar Panels:
Metal Core PCBs are used in the manufacturing of solar panels as supports and connections for solar cells. Metal Core PCBs provide structural stability to electronic components and enable the efficient transfer of current from the solar cell modules to other components. Additionally, the excellent thermal dissipation capabilities of Metal Core PCBs help maintain the working temperature of solar cells within the ideal range, enhancing energy conversion efficiency.
Other Application Areas:
Apart from the aforementioned fields, Metal Core PCBs find extensive applications in many other areas. For instance, they are used in high-power electronic devices, power modules, computer hard disk drives, medical equipment, aerospace electronics, and more. The thermal management and reliability characteristics of Metal Core PCBs make them the preferred choice for critical components in these industries.
Metal Core PCB offer significant advantages over traditional PCBs, particularly in terms of thermal management, durability, and compactness. Their unique construction incorporating a metal base layer makes them ideal for applications that require efficient heat dissipation and high-power handling capabilities.
As technology continues to advance, Metal Core PCBs are likely to play an increasingly important role in the electronics industry, enabling the development of more powerful, reliable, and compact electronic devices.