Silver plating plays an important role in electronic manufacturing. However, the common defect of "insufficient Tin" during the surface-mounting process poses numerous challenges for manufacturing companies. This issue primarily manifests as large solder pads lacking sufficient solder, while small solder pads meet quality standards. This article will delve into the reasons behind the "insufficient Tin" defect and propose comprehensive improvement suggestions to ensure a more stable and efficient surface-mounting process, contributing to the development of the electronics industry by delivering more high-quality products.
Understanding the "insufficient Tin" defect
Silver immersion plating plays a critical role in electronic manufacturing, especially in surface mount technology, as it serves as the bridge between electronic components and PCB boards. However, the common defect of "insufficient Tin" during the soldering process of silver immersion plating has always been one of the challenges faced by electronic manufacturing companies. This issue typically manifests as large solder pads lacking sufficient solder, while small solder pads meet quality standards. Such quality defects can lead to weak solder joints, causing electronic component failures, and even affecting the overall performance and reliability of the product.
Before delving into the "tin whiskers" defect, we must first understand some key foundational conditions.
Firstly, the thickness of the steel sheet in the steel mesh directly affects the surface mount process. Thinner steel sheets may result in uneven pressure of the solder paste, thereby affecting the distribution of solder on the pads.
Secondly, high-quality tin plating is crucial to ensure successful soldering, including solder height, volume, and area, which must fall within the acceptable range. To ensure quality, it is recommended to use SPI (Solder Paste Inspection) equipment for testing and to use premium solder paste brands like Alpha or Kester with 3.0% silver content.
Reason 1: Insufficient Welding Temperature
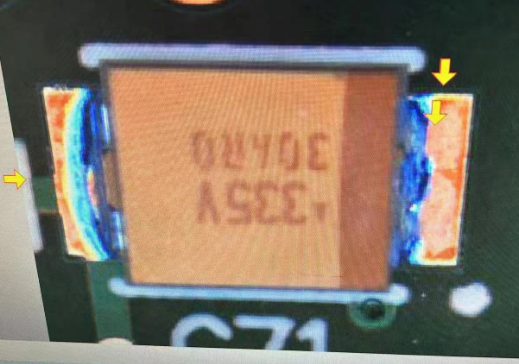
One of the main reasons for the "insufficient Tin" defect is that the large solder pad absorbs heat quickly, leading to insufficient welding temperature. The instability and non-uniformity of welding temperature can result in the incomplete melting of solder paste, thus failing to effectively wet the solder pad and pins, causing the phenomenon of "insufficient Tin."
To address the issue of insufficient welding temperature, we need to take the following measures.
Appropriately raise the welding temperature:
By adjusting the temperature curve during the welding process, it is recommended to moderately increase it by around 5°C on the existing furnace temperature to ensure the solder can fully melt. However, it is essential to be cautious as excessively high temperatures may lead to other issues, such as solder overflow or component damage. Therefore, it is necessary to conduct temperature testing and optimization carefully.
Adjusting the furnace temperature and time:
It is recommended to control the furnace temperature within the range of 240-245°C and make appropriate adjustments to the soldering time, usually between 60-90 seconds. Additionally, the reflow time can be moderately shortened to reduce the possibility of solder bridging, thereby minimizing the flow of solder from the large solder pads to the pins.
Through these improvement measures, we can effectively enhance the stability and uniformity of the welding temperature, thereby reducing the occurrence of the "insufficient Tin" phenomenon.
Reason Two: Silver Oxidation and Contamination
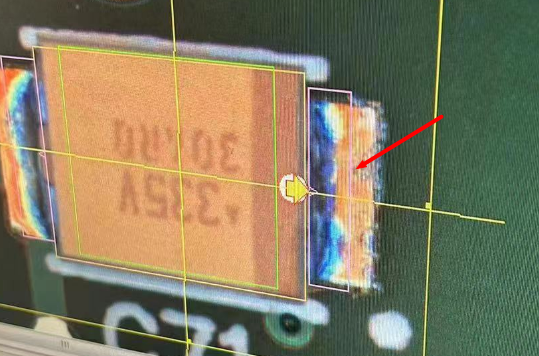
Silver, as a reactive metal, is prone to oxidation and contamination during the soldering process. This is another significant factor contributing to the "insufficient tin" defect. The oxidation on the surface of silver solder pads can affect the adhesion between solder paste and pads, reduce soldering quality, and consequently lead to inadequate soldering amounts.
To avoid the oxidation and contamination of silver, we should pay attention to the following points.
Control the placement time:
Once the package of the silver-plated board is opened, it should be placed into the SMT production as soon as possible, ideally within 12 hours, and no longer than 16 hours. This will ensure that the surface of the silver pads remains in good condition and reduces the likelihood of oxidation.
Avoid touching the surface of the board with bare hands:
Operators should refrain from directly touching the surface of the silver-plated board with their bare hands to prevent contamination and oxidation.
Maintain a constant temperature and humidity environment:
During the SMT (Surface Mount Technology) process, the silver-plated board should be placed in a constant temperature and humidity environment to preserve its surface stability. Constant temperature and humidity conditions help reduce oxidation and contamination of silver solder pads, ensuring the quality of the SMT.
Through the above measures, we can minimize the oxidation and contamination of the silver solder pads, thereby reducing the risk of "insufficient Tin" defects.
To comprehensively address the "insufficient Tin" defect issue on silver-plated boards, we should adopt the following integrated strategies.
Perform regular maintenance:
Ensure production equipment and tools are in good condition, conduct regular maintenance and upkeep of furnace temperature control equipment to ensure its stable operation.
Optimize process parameters:
Through continuous data analysis and production practices, optimize process parameters such as soldering temperature, time, and flow rate to find the best combination.
Train operators:
Enhance the training of operators, improve their awareness of "insufficient Tin" defects and their handling methods to reduce issues caused by operational mistakes.
Implement automation technology:
Consider introducing more advanced automation equipment to improve the stability and consistency of the SMT (Surface Mount Technology) process, reducing the impact of human factors on production quality.
Strengthen supply chain collaboration:
Establish close cooperation with solder paste suppliers to ensure supply stability and quality control.
The "insufficient Tin" defect in the silver-plating process is a common yet avoidable issue. By adjusting the soldering temperature and time, preventing silver pads from oxidation and contamination, and implementing comprehensive improvement strategies, we can effectively address this problem and enhance the quality and stability of surface mount technology.
Moreover, continuously exploring advanced technologies and management practices will drive the electronics manufacturing industry towards higher levels, contributing to its sustainable development. Through our collective efforts in minimizing the "insufficient Tin" defect, we can improve the reliability and performance of electronic products, meeting the ever-growing demand for high-quality products from consumers.
Furthermore, solving the "insufficient Tin" defect brings significant economic and commercial benefits to electronic manufacturing companies.
Firstly, it reduces the production of non-conforming products, lowering the risks of product recalls and customer complaints, thereby safeguarding the company's reputation and brand image.
Secondly, it enhances production efficiency and product quality, reducing losses and rework during the manufacturing process, ultimately lowering production costs and increasing the company's profitability.
In this fiercely competitive electronics industry, continuous improvement in surface mount technology is crucial. With technological advancements and market changes, we must closely monitor new materials, equipment, and the latest developments in surface mount technology. Only through continuous learning and adaptation can we maintain a competitive edge in the industry and drive progress in electronic manufacturing.
Transform Your PCB Manufacturing with
SprintPCBSprintPCB is a renowned high-tech enterprise specializing in delivering exceptional PCB manufacturing services to global clients. With our extensive industry knowledge and competitive pricing, you can shift your attention towards the most vital elements of your organization. Get in touch with us today to explore the potential for collaboration and experience how we can help you surpass your goals.