PCB assembly is a crucial step in the manufacturing process of electronic devices. In today's highly advanced technology industry, the efficiency and reliability of PCB assembly are crucial for the quality and performance of products. However, there are many challenges in the PCB assembly process, including complex electronic component placement, precise soldering requirements, and the need for quality control.
When facing these challenges, using the appropriate tools is crucial. The right tools not only improve assembly efficiency but also ensure the reliability and consistency of the assembly. Therefore, this article will introduce 10 essential tools that play a crucial role in efficient and reliable PCB assembly processes.
the solder paste printer for PCB assembly
First, we will introduce the first essential tool: solder paste printer. The solder paste printer is a specialized device used to print solder paste accurately and uniformly on PCBs, enabling reliable soldering of electronic components during the assembly process. Its main function is to scrape solder paste precisely over the pad positions on the template or stencil, ensuring even and compliant distribution of the solder paste.
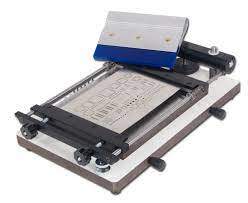
There are many benefits to using a solder paste printer. Primarily, it improves production efficiency. Compared to manually applying solder paste, a solder paste printer can quickly and accurately complete the entire PCB solder paste printing process. This saves a significant amount of time and labor, while meeting the demands of large-scale production.
Secondly, solder paste printers can improve the reliability and consistency of PCB assembly. Using a printer ensures uniform thickness and distribution of solder paste on each solder pad, reducing the possibility of soldering defects such as voids or short circuits. This helps improve assembly quality and reduce product failure rates.
Now let's look at some well-known solder paste printing machine brands and their price ranges:
DEK NeoHorizon 03ix: Priced approximately between $20,000 and $50,000.
DEK Horizon 03iX: Priced approximately between $15,000 and $30,000.
MPM Momentum Elite: Priced approximately between $25,000 and $50,000.
MPM Accela: Priced approximately between $15,000 and $30,000.
EKRA E5: Priced approximately between €20,000 and €40,000.
EKRA X5: Priced approximately between €25,000 and €50,000.
In addition to the solder paste printer, the pick-and-place machine is another crucial tool in the PCB assembly process. It works closely with the solder paste printer to ensure the accurate placement of electronic components and the completion of the soldering process. The combination of these two tools enables efficient and reliable PCB assembly.

the pick-and-place machine for PCB assembly
The pick-and-place machine is one of the crucial tools in the PCB assembly process. It is capable of quickly and accurately installing surface mount devices (SMD) onto the printed circuit board, significantly enhancing assembly efficiency and quality.
The function of a pick-and-place machine is to automatically select SMD components from the feeder and precisely place them at specified positions on the PCB, based on pre-set programs and data. It achieves efficient pick-and-place operations through the coordination of high-speed and precise mechanical arms, vision systems, and control software.
The SMT machine has the following advantages:
High speed and high precision
The SMT machine can perform surface mounting operations at a very high speed, processing thousands of components per minute. It also achieves precise positioning control, ensuring accurate installation of components on the PCB.
Automation and intelligence
The automation capability of the SMT machine enables it to automatically identify and correct the position and orientation of components, reducing human errors in operation. Its intelligent control software can also monitor and adjust parameters in real time during the surface mounting process, improving reliability and consistency.
Versatility
The SMT machine can accommodate various sizes and types of SMD (Surface Mount Device) components, ranging from tiny chip components to larger QFP (Quad Flat Package) and BGA (Ball Grid Array) devices. This versatility makes the SMT machine an ideal choice for various types of PCB assembly work.
Here are some common surface mount machine brands:
Siemens is a well-known supplier of electronic manufacturing equipment, and its surface mount machine product series include the Siplace D series and Siplace X series. The prices range from tens of thousands of dollars to hundreds of thousands of dollars, depending on the configuration and model.
Yamaha is also a famous surface mount machine manufacturer, and its product series include the YSM series and YS series. The prices range from thousands of dollars to hundreds of thousands of dollars, depending on the configuration and model.
Juki is another popular brand of surface mount machines, and its product series include the JX series and KE series. The prices range from thousands of dollars to hundreds of thousands of dollars, depending on the configuration and model.
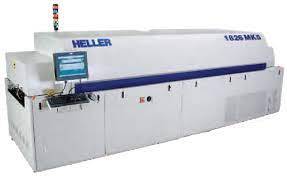
Next, we will introduce the reflow soldering oven, which is a critical equipment for soldering after the surface mount process. The reflow soldering oven can join the surface mount components with the PCB, ensuring the reliability and stability of electrical connections. Let's continue to learn about the functions and importance of the reflow soldering oven.
the reflow soldering oven for PCB assembly
Reflow soldering oven is a critical tool used to correctly connect electronic components to PCBs. By controlling temperature and heating profiles, it melts solder paste at high temperatures, securely soldering electronic components onto the printed circuit board. Reflow soldering ovens play a crucial role in the PCB assembly process as they provide precise temperature control and uniform heating, ensuring reliable and high-quality solder joints.
There are many well-known brands of reflow soldering ovens available in the market. Here are a few brands and their approximate price ranges:
Juki RS-1 reflow soldering oven: priced at around $20,000 to $30,000. It is a high-performance reflow soldering oven with advanced temperature control and a multifunctional operating interface, suitable for high-precision and efficient PCB assembly.
Heller 1809 MK5 reflow soldering oven: priced at approximately $15,000 to $25,000. This model features an innovative heating system and a programmable controller, allowing for precise temperature configurations and quick heating cycle times.
BTU Pyramax reflow soldering oven: roughly priced between $40,000 to $50,000. It is a high-end reflow soldering oven that utilizes advanced hot air circulation technology and multiple temperature zone control, enabling higher production efficiency and soldering quality.
With the development of the PCB assembly industry, reflow soldering technology has been continuously improving, and new innovative equipment keeps emerging. However, merely having an advanced reflow soldering furnace is not enough to guarantee efficient and reliable PCB assembly. Another essential tool is a hot air gun, which plays a crucial role in tasks such as soldering, heat shrinking, and rework.
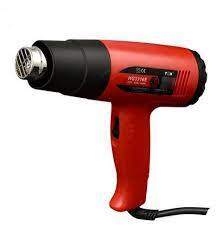
Next, we will explore the role of a heat gun and the differences between heat guns of various prices.
the heat gun for PCB assembly
A heat gun is a commonly used tool for soldering, heat shrinking, and component removal tasks in the PCB assembly process. It generates a high-temperature air flow to melt solder joints or shrink heat shrink tubing, thus achieving reliable connections and packaging. The following is a detailed description of the heat gun and the differences between heat guns of different prices.
The working principle of a heat gun is to guide the current to the heating element, causing it to generate heat, and then discharge the heat through a nozzle, forming a hot air flow. Heat guns typically have adjustable temperature and airflow controls to accommodate different assembly tasks and material requirements.
When choosing a heat gun, price is an important factor to consider. Heat guns of different prices usually have different features and performance. Here are the differences between heat guns in several common price ranges.
Economy-level heat guns:
These heat guns are usually priced lower and are suitable for beginners or infrequent users. They typically have lower power and fewer functions, such as fixed temperature and fan speed settings.
Mid-range heat guns:
Mid-range heat guns offer a balance between price and performance. They usually have higher power, multiple temperature, and fan speed settings to meet different needs. Some mid-range heat guns may also have additional features like built-in thermometers and automatic shut-off.
High-end heat guns:
High-end heat guns have higher prices and are suitable for professional users and demanding assembly tasks. They usually have higher power, precise temperature control, and multiple fan speed modes for fine-tuned operations. High-end heat guns may also have advanced safety features and user-friendly interfaces.
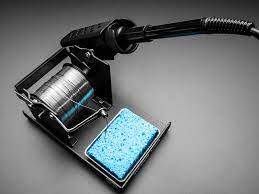
the soldering stations and stands for PCB assembly
During PCB assembly, soldering stations and stands are essential tools. They provide assembly personnel with a stable work platform and a convenient operating environment. They can help ensure soldering quality and alleviate operator fatigue.
A soldering station is a flat and sturdy surface, typically made of metal, used for placing PCBs, components, and soldering tools. The main function of a soldering station is to provide a stable working area, making the soldering process more precise and controllable.
The flat surface and sturdy structure of the soldering station ensure that the PCB does not shake or move during the soldering process, providing better soldering stability.
Soldering stations typically have good thermal conductivity, which helps to evenly distribute soldering heat and reduce issues like heat damage or cold solder joints.
Some advanced soldering stations are also equipped with rulers, scale lines, or fixed fixtures to assist in precise positioning of components and PCBs, ensuring soldering accuracy and consistency.
A holder is a device used to secure the PCB and components in place, maintaining stability and the correct position during soldering. Holders can come in various types and designs, including adjustable holders, clamp holders, and magnetic holders.
The fixture holds or secures the PCB and components, ensuring their stability during the soldering process and avoiding soldering deviations or quality issues caused by instability.
The fixture provides an ergonomic working environment for soldering, concentrating the soldering focus on the necessary areas and reducing operator fatigue and the likelihood of soldering errors.
Some fixtures have adjustable features to accommodate PCBs and components of different sizes and shapes, offering greater flexibility and adaptability.
By using welding tables and fixtures, assembly personnel can focus and be more precise during the welding process, thereby improving welding quality and efficiency. These tools not only provide stability and accuracy but also reduce the risks of welding errors and damages, thus enhancing overall reliability in PCB assembly.
Next, let's move on to the next tool, namely quality inspection equipment. This tool complements welding tables and fixtures and provides necessary support and assurance to ensure assembly quality.
quality inspection instruments for PCB assembly
In the efficient and reliable process of PCB assembly, quality inspection instruments play a crucial role. They ensure that the assembled circuit boards meet high-quality standards and promptly identify and correct any potential issues. Here are some commonly used qualities inspection instruments.
Microscopes are key tools used to examine the details of tiny components and solder connections on circuit boards. By magnifying the image, you can inspect the quality of solder joints, accuracy of component placement, and integrity of surface mount devices. High-quality microscopes are equipped with appropriate lighting and magnification capabilities, allowing you to observe details clearly and perform accurate inspections.
X-ray inspection equipment is a non-invasive testing tool used to assess the reliability of solder connections and detect hidden defects. It can penetrate the surface of circuit boards and provide detailed information about solder joints, solderability, and concealed internal structures. X-ray inspection equipment can help you identify potential soldering issues such as cold solder joints, shorts, and voids, enabling timely measures for repair.
Infrared thermal imaging cameras can assist in detecting hotspots and thermal distributions on circuit boards, thereby identifying potential thermal issues and thermal runaway phenomena. Through infrared thermal imaging technology, you can identify overheated components, areas with poor thermal conductivity, and regions of concentrated heat. This is crucial for ensuring the stability, durability, and reliability of the circuit board.
In addition to visual inspection, the use of various electronic testing equipment is also an important step in quality inspection. These devices can be used to measure parameters such as resistance, capacitance, voltage, etc., on circuit boards to ensure the correctness of components and connections.
Common electronic testing equipment includes multi-purpose testers, logic analyzers, spectrum analyzers, and so on. By conducting comprehensive electronic testing on circuit boards, you can verify whether their performance and functionality meet expectations.
By using these quality inspection instruments, you can ensure that the assembled PCB meets the required standards and avoid potential faults and issues. Moreover, these tools also help improve the efficiency and reliability of the assembly process.
Now, let's turn our attention to automated testing equipment. Automated testing equipment is closely related to quality inspection instruments, and both works together to improve the efficiency and reliability of PCB assembly. Let's explore the role of automated testing equipment and how it complements the quality inspection instruments.
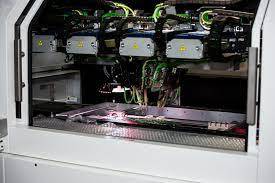
automated testing equipment for PCB assembly
In the process of PCB assembly, quality control and testing are crucial stages. To ensure the reliability and performance of the PCB, the use of automated testing equipment is essential.
Automated testing equipment enables efficient and accurate functional and electrical testing to verify the proper operation of the PCB. These devices are typically equipped with advanced testing instruments and software that can automatically perform various testing tasks, such as electrical connectivity testing, power analysis, and signal integrity testing.
By using automated testing equipment, manufacturers can significantly improve the speed and accuracy of testing, thereby reducing time to market and minimizing failure rates. They can quickly scan and identify potential defects or faults, providing timely feedback and reports for repair or adjustment purposes.
The benefits of using automated testing equipment are not only to improve production efficiency and quality but also to save labor resources and reduce human errors. With the automation of the testing process, factors such as human intervention and subjective judgments are minimized, making the test results more objective and reliable.
As one of the important tools to improve PCB assembly efficiency and reliability, automated testing equipment provides manufacturers with comprehensive testing capabilities. However, even with the most advanced testing equipment, defects during the assembly process can still lead to issues.
Therefore, ensuring the quality and correctness of the components before assembly is crucial. The next tool to be introduced is electrostatic discharge (ESD) protection equipment, which ensures the stability and quality of the assembly process.
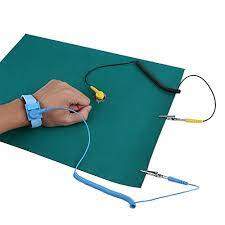
static protection tools for PCB assembly
Static protection tools play a critical role in the PCB assembly process. Due to the high sensitivity of electronic components on PCBs to static electricity, electrostatic discharge can cause component damage or malfunction. Therefore, it is crucial to take appropriate static protection measures.
One common static protection tool is a wrist strap. Wrist straps are typically made of conductive material and are used to connect the operator's body to the ground, effectively dissipating static electricity from the human body to the ground. This helps prevent static discharge during PCB handling and protects sensitive electronic components.
In addition, there is also an anti-static mat. An anti-static mat is a conductive pad that is typically placed on a workbench. It effectively guides static electricity from the PCB and the operator to the ground, reducing the risk of static discharge. The anti-static mat also provides a stable working surface to prevent PCB sliding and damage.
Anti-static gloves are also essential tools. These gloves are usually made of conductive materials and can prevent the accumulation of static electricity on the hands, protecting sensitive electronic components from static discharge damage. Choosing the appropriate anti-static gloves ensures that the operator maintains good grounding and protection during the PCB assembly process.
To further enhance static protection, some anti-static tools are equipped with static eliminators or static controllers. These devices neutralize static electricity by emitting opposite charges, reducing the accumulation and discharge risks of static electricity.
Correct labels and markings are crucial before proceeding with PCB assembly. They can assist operators in accurately identifying and locating different components, connections, and functionalities.
Labels and marking tools play an important role in efficient and reliable PCB assembly processes. They can aid engineers and technicians in accurately identifying and recognizing different components, circuits, and connections, thereby improving assembly efficiency and traceability.
Labels and marking tools can take various forms, including adhesive labels, permanent markers, color coding, and more. They can be applied to components, circuits, and connection points on the PCB board for identification purposes during the assembly process or for future maintenance and troubleshooting.
labels and marking tools for PCB assembly
Here are several important applications of labels and marking tools:
Component identification: During the assembly process, labels and marking tools can be used to identify different components such as resistors, capacitors, integrated circuits, and so on. By attaching labels or using marking pens on the components, operators can quickly recognize and distinguish the type, value, and orientation of each component.
Circuit labeling: Labels and marking tools can also be used to identify and mark different circuits on PCB boards. By adding labels to each circuit or marking them with a marking pen, engineers and technicians can quickly understand the layout and connectivity of the circuit board. This is helpful for circuit inspection, debugging, troubleshooting, and subsequent maintenance.
Node marking: In complex PCB layouts, the identification and marking of nodes are crucial. Labels and marking tools can be used to accurately mark the location, type, and function of the connection points. This allows assemblers to easily locate and correctly connect the corresponding components or circuits.
Traceability: Labels and marking tools also play an important role in providing traceability. By adding unique identification codes or serial numbers to each assembled PCB board, the manufacturing process, component sources, and test results of each board can be tracked. Such traceability is crucial for quality control, troubleshooting, and product recall.
The proper use of labels and marking tools can greatly simplify the PCB assembly process and improve overall efficiency and reliability. However, relying solely on labels and marking tools is not enough to guarantee high-quality PCB assembly. In addition to good identification and marking, other tools and processes are required to ensure proper soldering, quality control, and testing.
cleaning and maintenance tools for PCB assembly
Next, we will discuss the tenth essential tool: cleaning and maintenance tools. These tools can help you keep the PCB board clean, maintain it, and ensure its long-term reliability. Let's continue to learn about the importance and uses of these tools.
It is crucial to maintain cleanliness and proper maintenance of tools during PCB assembly. These tools not only ensure efficiency and reliability during the assembly process but also extend the lifespan of the tools. Here are some commonly used cleaning and maintenance tools.
Brush: Choose a soft yet resilient brush to remove dust, debris, and residues from the surface of PCBs and assembly tools. This helps to prevent short circuits and other quality issues in the conductive paths. When using the brush, make sure to handle it gently to avoid damaging the PCB or other components.
Vacuum Cleaner: Use an electrostatic-sensitive vacuum cleaner to clean the workspace and eliminate dust and debris. Electrostatic-sensitive vacuum cleaners prevent damage to electronic components and PCBs caused by static electricity.
Cleaning Solvent: Select a cleaning solvent suitable for PCB assembly to remove grease, dirt, and solder residues. Note that different types of PCBs and components may require different cleaning solvents. Make sure to choose a solvent that is suitable for the specific materials and follow the manufacturer's recommendations for use.
ESD (Electrostatic Discharge) Protection Equipment: Use appropriate ESD protection equipment, such as antistatic gloves and wrist straps, during the cleaning and maintenance process. This effectively prevents damage to sensitive electronic components and PCBs caused by static electricity.
Lubricant: For mechanical parts that require lubrication, using the appropriate lubricant ensures their proper functioning and lifespan. Choose a non-conductive lubricant to avoid affecting the performance of electronic components and PCBs.
By regularly cleaning and maintaining your tools, you can keep them in good condition, extend their lifespan, and ensure their reliability. Additionally, this helps reduce errors and quality issues caused by dirty tools.
During the PCB assembly process, the use of appropriate tools is crucial for achieving efficient and reliable results.
Through the 10 tools introduced in this article, we can see their key roles in different stages of PCB assembly. From the precise coating of solder paste by the stencil printer to the high-speed and accurate placement by the pick-and-place machine, and the optimized soldering in the reflow oven, these tools greatly enhance the efficiency and quality of the assembly.
Additionally, tools such as heat guns, soldering stations, and fixtures provide stability and convenience, making the soldering and debugging processes smoother.
Quality inspection instruments and automated testing equipment help us ensure assembly quality and functional integrity. ESD protection tools safeguard electronic components from electrostatic damage, while labeling and marking tools, as well as cleaning and maintenance tools, contribute to maintaining traceability and keeping the equipment in good condition.
In conclusion, selecting the appropriate tools is key to achieving efficient and reliable PCB assembly.
SprintPCB: Your Reliable PCB Support ProviderSprintPCB is a renowned high-tech enterprise offering comprehensive PCB manufacturing services to clients globally. With our extensive expertise and cost-effective solutions, you can prioritize your organization's critical requirements while enjoying a seamless process. Get in touch with us today and discover how we can assist you.