With the continuous growth in demand for high-quality medical PCBs in the healthcare industry, the field is facing numerous challenges. This article delves into these challenges, focusing on key considerations when designing and producing medical PCBs to ensure the reliability and safety of medical devices.
Additionally, we will explore the standards that medical PCBs must meet and provide essential factors to consider when selecting PCB suppliers. The aim is to drive innovation in the healthcare sector and explore emerging trends in medical PCB technology.
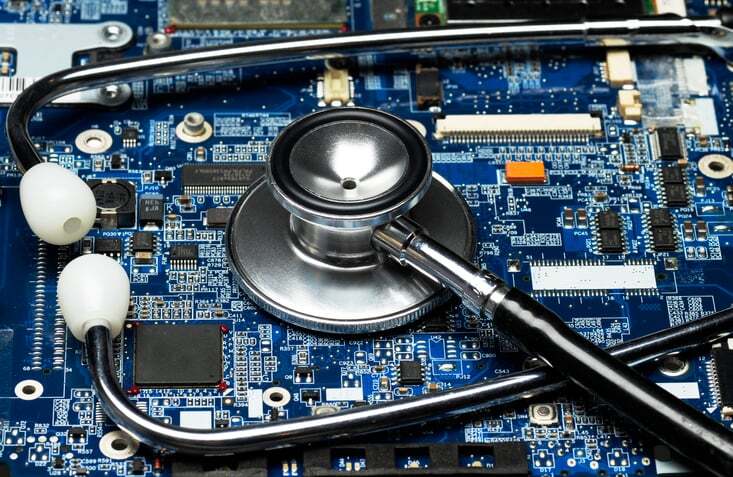
Challenges in the Medical Industry and Medical PCBs
Method Validation:
In the medical industry, accurate data and results are crucial for the health and well-being of patients. Therefore, the performance of medical PCBs must undergo rigorous method validation to ensure their accuracy and reliability in medical devices. The validation process involves employing scientific methods and rigorous testing to verify whether the medical PCB complies with design specifications and performance requirements.
For instance, let's consider a medical device designed to monitor a patient's electrocardiogram (ECG) activity and transmit the data to a monitoring unit through a medical PCB. In this scenario, method validation would involve sending simulated ECG signals to the medical PCB and ensuring that the PCB accurately converts and transmits the data. By comparing the validated data with the expected data, we can determine the accuracy and stability of the medical PCB under normal operating conditions.
Facility Approval:
The production facilities for medical PCBs must adhere to strict approval standards to ensure the reliability and quality of the manufacturing process. These approval standards typically encompass the cleanliness of the facilities, employee training, quality management systems, and environmental management measures. The manufacturing and assembly of medical equipment needs to be conducted in controlled environments to prevent potential contamination or defects.
Simultaneously, an approved medical PCB manufacturer ensures that its production facilities are in excellent condition, with each production step monitored and recorded. Staff members receive training to ensure the proper operation of equipment and adherence to best practices. Furthermore, the facility is equipped with advanced environmental control systems to maintain stable temperature and humidity levels throughout the production process.
Part Limitations:
Medical devices are often constrained by the use of specific components, which may include particular models of components, sensors, or integrated circuits. Medical PCB designs must accommodate these part limitations and ensure compatibility with other components. Additionally, these components typically need to exhibit high reliability and long-term availability.
If a medical device manufacturer relies on specific models of sensors to monitor patients' physiological parameters, the medical PCB designer must ensure that the PCB can interface correctly with these sensors and facilitate error-free data transmission. Moreover, considering that medical devices usually have long lifecycles, the medical PCB designer must also ensure that the chosen components have a reliable long-term supply.
High Production Costs:
The production of medical PCBs typically requires a high level of technical expertise and stringent quality control, which can result in higher production costs. The medical industry demands exceptional quality and safety standards, necessitating additional resources and labor for manufacturing medical PCBs.
Due to the need for strict quality standards and validation processes, the manufacturing of medical PCBs may require additional equipment and tools to ensure compliance. Moreover, employees need to undergo extensive training to ensure they can operate the equipment correctly and adhere to quality control procedures. All these factors can contribute to higher production costs for medical PCBs, but they are a necessary investment to ensure the safety and performance of medical devices.
As an essential component of medical devices, the performance and quality of medical PCBs directly impact patient safety and the stable operation of medical equipment. Hence, understanding and overcoming these challenges, as well as prioritizing key factors in the design and production of medical PCBs, play a critical role. Next, we will delve into these challenges and crucial considerations to ensure medical devices are supported by high-quality medical PCBs.
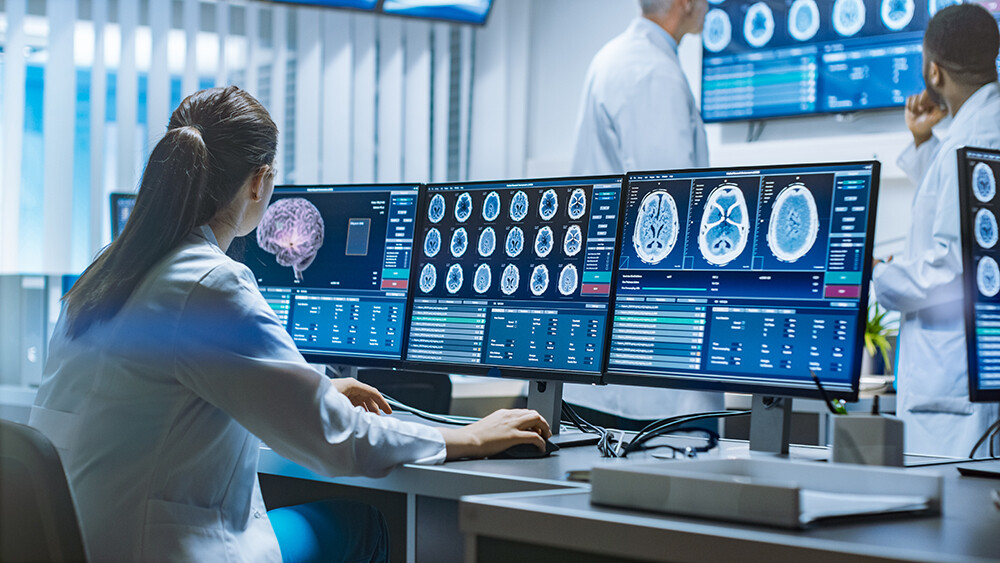
Key Considerations in Designing and Manufacturing Medical PCBs
Signal Integrity:
In medical devices, accurate signal transmission is crucial for patient safety and diagnostic outcomes. Therefore, in the design and production of medical PCBs, special attention must be given to signal integrity. This involves avoiding signal losses, cross-interference, and timing issues. For instance, in the case of high-frequency signals, the routing and traces on the medical PCB must precisely control impedance to ensure the accurate transmission of signals.
EMI/EMC Compliance:
Electromagnetic Interference (EMI) and Electromagnetic Compatibility (EMC) are crucial considerations in medical device design. Medical PCBs must be capable of effectively shielding and suppressing interference signals to ensure the stable operation of the equipment and prevent interference with other devices. For instance, incorporating appropriate grounding techniques and electromagnetic shielding layers can significantly reduce EMI.
Power Consumption:
Medical devices often require continuous operation for extended periods or rely on battery power. Therefore, efficient power management in medical PCBs is of utmost importance. When designing medical PCBs, it is essential to use low-power electronic components and circuits to extend the device's battery life. For example, utilizing low-power microcontrollers and optimizing power management circuits can significantly reduce power consumption.
Design for Manufacturing (DfM):
Considering the feasibility of manufacturing during the design phase is crucial for the successful production of medical PCBs. Design for Manufacturing (DfM) of medical PCBs can help optimize the design, simplify the production process, and reduce manufacturing costs. For instance, considering the board layer layout and component placement in the PCB design can avoid unnecessary manufacturing issues and adjustments.
High Reliability:
The reliability of medical devices is paramount for patient safety and healthcare outcomes. Medical PCBs must undergo rigorous reliability testing to ensure they do not fail during long-term usage. For example, using high-quality components, precise soldering, and implementing a sound fault diagnosis process can enhance the reliability of medical PCBs.
Quality Control:
The production process of medical PCBs must comply with stringent quality control standards to ensure that each PCB meets the design specifications. During the manufacturing process, rigorous quality checks and testing are essential to eliminate potential manufacturing defects. For instance, employing Surface Mount Technology (SMT) assembly techniques and Automated Optical Inspection (AOI) systems for automated inspection can significantly enhance the efficiency of quality control.
Traceability:
The medical industry requires complete traceability for all components to trace potential manufacturing issues and enable backward tracking. Medical PCBs must accurately record the origin and production process of each component for traceability when necessary. For example, utilizing unique identifiers and recording data of the production process can facilitate traceability for medical PCBs.
Material Selection:
Selecting appropriate materials is crucial for the performance and reliability of medical PCBs. Specific requirements and environmental factors of medical devices must be taken into consideration when choosing the right materials. For instance, special high-temperature resistant or chemically resistant materials may be used in medical devices to adapt to specific operating conditions.
Environmental Controls:
Medical devices often operate in harsh environmental conditions, and medical PCB designs must incorporate measures to adapt to these conditions. For example, in high-humidity or high-temperature environments, medical PCBs must have features such as moisture resistance, heat dissipation, and dust protection.
Testing and Validation:
Testing and validation are indispensable steps in the design and production process of medical PCBs to ensure their performance and quality. Comprehensive functional testing, reliability testing, and environmental testing can ensure that medical PCBs perform exceptionally well under various working conditions.
For instance, using high-precision testing instruments and simulation tools can validate the performance of medical PCBs during the design phase and minimize potential issues in subsequent testing.
When designing and producing medical PCBs, it is crucial to consider multiple factors to ensure the performance and reliability of medical devices. Signal integrity, electromagnetic interference and compatibility, power optimization, and other key factors require careful investigation.
Additionally, quality control, material selection, and environmental adaptability are equally important. The design for manufacturability (DfM) of medical PCBs is also one of the critical factors for successful outcomes. In-depth understanding and attention to these factors can significantly enhance the quality and performance of medical PCBs.
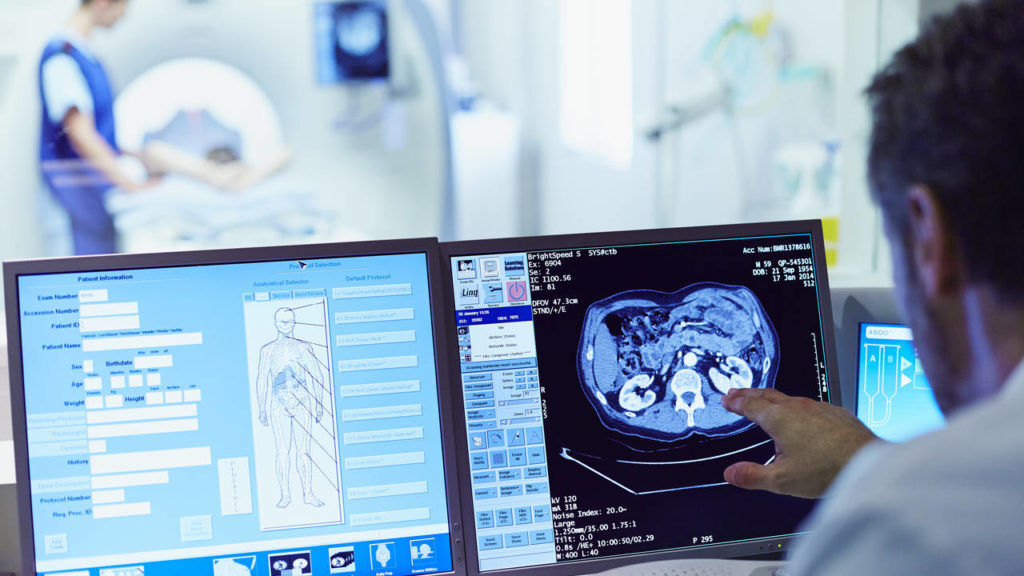
Standards of Medical PCBs
Medical PCBs must comply with a series of strict international and industry standards to ensure the safety and performance of medical devices. These standards represent crucial requirements imposed by the medical industry on the design and production of medical PCBs, aiming to safeguard patient safety and ensure reliable operation of medical equipment. Compliance is of paramount importance for manufacturers, healthcare professionals, and end-users in the field of medical devices.
In the following section, we will delve into some of the key standards that medical PCBs must adhere to.
ISO 13485: Medical Device Quality Management System Standard
ISO 13485 is an international standard widely followed in the global medical device industry. It sets forth the requirements that medical device manufacturers must adhere to in terms of quality management.
For medical PCB manufacturers, compliance with ISO 13485 forms the foundation for ensuring the quality and reliability of medical PCBs. These standards mandate that manufacturers establish and implement a quality management system covering various stages throughout the entire lifecycle, from design and development to production, installation, and servicing.
By complying with ISO 13485, medical PCB manufacturers can effectively control the production process, minimize potential risks and quality issues, and ensure the safety and performance of medical devices.
IEC 60601: Medical Electrical Equipment Safety Standard
IEC 60601 is an international standard applicable to medical electrical equipment. It imposes stringent requirements on the electrical safety, electromagnetic compatibility (EMC), and environmental adaptability of medical devices.
For medical PCB manufacturers, compliance with IEC 60601 is a crucial means to ensure that medical PCBs meet international standards in terms of electrical safety and EMC. This standard defines the electrical safety requirements that medical devices must meet to prevent electrical shocks and other electrical hazards.
Additionally, it specifies limitations on electromagnetic interference to ensure that medical PCBs can operate properly in electromagnetic environments without causing interference to other devices.
60601: Medical Electrical Equipment Safety Standard
UL 60601 is the medical electrical equipment safety standard in the United States, similar to IEC 60601 but specific to the US market. The UL standard is commonly used for certification and testing of medical devices.
For medical PCB manufacturers, ensuring PCB compliance with UL 60601 is a necessary requirement to enter the US market. Through UL certification, medical PCB manufacturers can demonstrate that their products meet the US safety standards, thereby increasing their market competitiveness and gaining trust from users and regulatory authorities.
RoHS Directive: Restriction of Hazardous Substances Directive
The RoHS Directive is an EU regulation aimed at environmental protection for electronic and electrical equipment. This directive restricts the use of hazardous substances, such as lead, mercury, cadmium, hexavalent chromium, in medical devices and PCBs.
Medical PCB manufacturers must ensure that their products comply with the requirements of the RoHS Directive to protect the environment and user health. Additionally, RoHS compliance enhances the competitiveness of medical PCB manufacturers in the European market.
These standards are just a part of the requirements that medical PCBs must comply with, as there are various other national and industry standards to consider. Compliance with these standards is not only an essential regulatory requirement for medical PCB manufacturers but also crucial to ensuring the safety and performance of medical devices, promoting the development of the medical industry, and safeguarding the well-being of patients.
Key Considerations When Choosing a PCB Supplier
Selecting the right PCB supplier is crucial for the successful design and production of medical PCBs. Not only does it ensure the quality and performance of medical devices, but it also helps reduce production costs and provides excellent service and support. When choosing a supplier, the following are key considerations that contribute to the smooth manufacturing and final delivery of medical PCBs.
Technical Capabilities and Experience:
The primary factor to consider is the supplier's technical capabilities and experience. An excellent PCB supplier should possess advanced technical equipment and a skilled technical team capable of meeting the specific requirements and complex designs of medical PCBs. Look for suppliers with extensive experience in the medical industry as they are more likely to understand the demands of medical equipment and offer feasible solutions.
Quality Control Process:
The quality and reliability of medical PCBs are crucial for patient safety. Suppliers should have strict quality control processes in place to ensure that each PCB complies with design specifications and standards. Understanding the supplier's quality management system, such as whether they hold certifications like ISO 13485, is a vital reference for assessing their quality control capabilities.
Certification and Compliance:
The medical industry has stringent requirements for product certification and compliance. Ensuring that the chosen PCB supplier meets international certification requirements, such as the Medical Electrical Equipment Safety Standard (IEC 60601), helps to reduce risks and ensure the safety of medical devices.
Supplier's Reputation and Reputation:
The reputation and standing of the supplier are crucial factors in selecting the right supplier. Seeking out suppliers with a good reputation and a history of successful collaborations with clients can enhance the smoothness and reliability of the partnership.
Services and Support Provided:
Throughout the entire manufacturing process, the services and support offered by the supplier are of utmost importance. Considering whether the supplier can provide timely technical support and after-sales services, as well as their ability to respond quickly and address issues, is essential.
Cost and Delivery Time:
Cost is one of the critical factors that must be considered when choosing a supplier. Understanding the supplier's quotation and payment terms is essential to ensure that the prices are reasonable and within budget. Additionally, the supplier must be able to deliver medical PCBs on time to maintain production schedules and supply chain stability.
Traceability and Transparency:
The medical industry demands strict traceability, requiring complete trace records for all components. Suppliers should provide clear transparency to ensure that the materials and processes they offer can be traced and verified.
Considering the factors mentioned above, selecting the appropriate PCB supplier will lay a solid foundation for the design and production of medical PCBs, ensuring high quality and reliability of medical devices. A reliable supplier is not only a business partner but also a key driving force behind innovation and development in the medical industry.
The medical industry has been experiencing a growing demand for high-quality medical PCBs. When designing and producing medical PCBs, it is crucial to thoroughly consider key factors such as signal integrity, compliance, power consumption, reliability, and quality control.
Adhering to international standards and selecting appropriate suppliers are essential steps to ensure the safety and performance of medical devices. The continuous innovation and optimization of medical PCB technology will present numerous opportunities and breakthroughs for the future of the healthcare sector.
SprintPCB is a renowned high-tech enterprise specializing in delivering exceptional PCB manufacturing services to global clients. With our extensive industry knowledge and competitive pricing, you can shift your attention towards the most vital elements of your organization. Get in touch with us today to explore the potential for collaboration and experience how we can help you surpass your goals.