In the field of electronics manufacturing, soldering technology is one of the key steps in connecting electronic components. Immersion Tin technology, as an important surface treatment method, is widely used in the manufacturing of Printed Circuit Boards (PCBs).
Immersion Tin involves replacing copper (Cu) with tin (Sn) on the surface of solder pads, resulting in the deposition of a copper-tin (CuSn) metallic compound on the surface. This article will explore the advantages, disadvantages, and applications of Immersion Tin technology in electronic manufacturing.
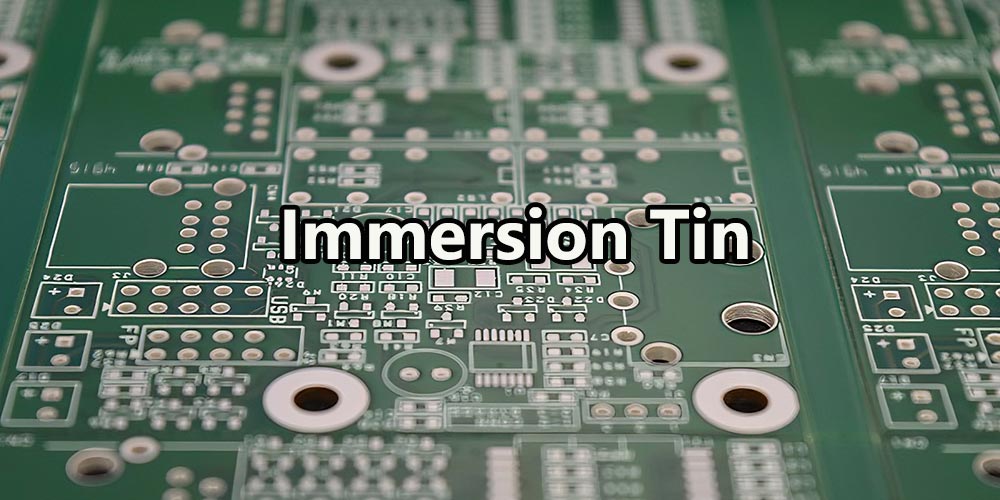
What is Immersion Tin?
Immersion Tin is a surface treatment technique widely used in electronic manufacturing. It involves replacing copper (Cu) with tin (Sn) on the surface of Printed Circuit Boards (PCBs) solder pads, resulting in the deposition of a copper-tin (CuSn) metallic compound on the surface. The Immersion Tin process not only provides good solderability but also forms a smooth coating on the solder pad surface, meeting the requirements of modern electronics manufacturing for high-precision component assembly.
Advantages of Immersion Tin
The widespread application of the Immersion Tin process in electronic manufacturing is due to its excellent solderability, flat surface, versatility, and environmental friendliness, among other advantages.
Excellent Solderability
The Immersion Tin process stands out in electronic manufacturing due to its outstanding solderability. When electronic components need to be connected, the soldering process is crucial. The Immersion Tin process ensures the stability of the soldering process by forming a thin layer of copper-tin metallic compound on the surface of solder pads. This metallic compound layer possesses excellent soldering characteristics, quickly melting and forming robust solder joints with other metal surfaces. This ensures reliable connections between electronic components, thereby enhancing product performance and long-term reliability.
Superior Surface Flatness
The Immersion Tin process can create a surface on solder pads similar to that of electroless nickel immersion gold (ENIG) process. In the process of electronic component assembly, a flat solder pad surface is crucial for the proper placement of components. This flatness not only helps ensure the precise positioning of components but also aids in reducing stress concentration, thereby enhancing the stability of solder joints and the overall performance of the product.
No Need for Metal Barrier Layer
The Immersion Tin process does not require the application of a metal barrier layer before soldering. In comparison to certain other soldering methods, such as Hot Air Solder Leveling (HASL) process, Immersion Tin does not necessitate the addition of extra metal materials, thereby reducing costs and simplifying the manufacturing process.
Suitable for Miniaturized Components
In modern electronic manufacturing, electronic components are becoming increasingly miniaturized. One of the advantages of the Immersion Tin process is its suitability for connecting miniature components, which may have finer pin arrangements and smaller solder pad sizes. The Immersion Tin process can create a uniform metallic compound layer on tiny solder pads, ensuring reliable connections for small-scale components.
Environmental Friendliness
Compared to certain surface treatment methods that involve harmful substances, such as gold plating, the Immersion Tin process is generally more environmentally friendly. It does not generate harmful wastewater or exhaust gases, thereby reducing its impact on the environment.
Disadvantages of Immersion Tin
Despite its good solderability and surface flatness, the Immersion Tin process has drawbacks that need to be carefully considered in practical applications, including short storage time, tin whisker formation, and issues related to soldering reliability.
Short Storage Time
A significant drawback of the Immersion Tin process is that the tin plating on solder pad surfaces is susceptible to oxidation, leading to limitations in storage time. Oxidation can result in the formation of tin oxide layers, which may reduce the solderability of the joints. This effect is particularly pronounced in high-temperature and high-humidity environments, where oxidation occurs at an accelerated rate, further exacerbating the short storage duration. Prolonged storage can lead to a decrease in solder joint quality, thereby impacting soldering reliability.
Tin Whisker Formation
During the Immersion Tin soldering process, a phenomenon known as tin whisker formation often occurs, where tiny tin fibers grow on the surface of solder pads.
These tin whiskers can potentially dislodge in the operational environment, leading to short circuits or other malfunctions between electronic components. The generation of tin whiskers is a result of the interaction between tin and copper on the solder pad surface, which can become more pronounced under certain specific conditions, thereby affecting solder joint stability.
Soldering Reliability Issues
A key concern in Immersion Tin soldering is tin migration, where tin on the surface of solder pads can move due to the effects of current or temperature. This can lead to changes in the shape and connection of solder joints, subsequently affecting the electrical connections between components.
Tin migration can result in issues like solder joint fractures, short circuits, and more, thereby diminishing product reliability. This phenomenon is particularly pronounced in high-temperature and high-humidity environments, demanding special attention and control.
Applications of Immersion Tin
The Immersion Tin process plays a crucial role in various application areas within the field of electronic manufacturing. From PCB manufacturing to surface mount technology and extending to multi-layer PCB interconnections and communication equipment production, the Immersion Tin process provides vital connectivity solutions for the reliability and performance of electronic products.
With ongoing technological advancements, the Immersion Tin process is poised to continue its significant role in electronic manufacturing, offering enduringly reliable connectivity solutions for a wide range of application domains.
Printed Circuit Board (PCB) Manufacturing
The Immersion Tin process is a common surface treatment method in PCB manufacturing. It is widely used for treating solder pads to ensure reliable connections of electronic components.
The Immersion Tin coating on solder pads provides excellent solderability, allowing solder to evenly distribute and form robust solder joints on component surfaces. This is crucial in various electronic devices, including communication equipment, computers, consumer electronics, and industrial control systems, among others.
Surface Mount Technology
The Immersion Tin process also plays a significant role in surface mount technology. It is utilized for connecting various surface-mounted components, such as chips, resistors, capacitors, diodes, and connectors. By forming an Immersion Tin coating on the pins of these components, reliable soldering connections can be achieved, securely affixing these components to the PCB.
Multi-Layer PCB Interconnections
The Immersion Tin process is also commonly used for interconnecting multiple layers of PCBs through the use of Plated Through Hole (PTH) technology. By applying an Immersion Tin coating inside the via holes, it ensures the transmission of signals and power between different layers, enabling efficient connectivity in complex circuit boards.
Communication Equipment
Due to the robust solder joints and excellent solderability provided by the Immersion Tin process, it finds extensive application in the manufacturing of communication equipment. This includes mobile phones, network routers, base stations, satellite communication devices, and more.
Consumer Electronics
The Immersion Tin process also plays a crucial role in the manufacturing of consumer electronic products, such as flat-screen televisions, audio devices, household appliances, and gaming consoles, among others. The production of these products requires high-quality connections to ensure performance and stability.
The Immersion Tin process, as an important surface treatment method, plays a significant role in electronic manufacturing. Despite its excellent solderability and surface flatness, challenges such as short storage time, tin whisker formation, and soldering reliability issues still need to be considered.
When applying the Immersion Tin process, manufacturers need to carefully weigh its advantages and disadvantages and take appropriate measures to ensure soldering quality and product reliability. With the continuous advancement of electronic technology, the Immersion Tin process is expected to further improve, providing the electronics manufacturing industry with even more reliable connectivity solutions.
Trust
SprintPCB to let your creativity shine on the world stage. Our professional team will go above and beyond to meet your PCB needs and ensure your design stands out in terms of quality and performance. Whether you are an electronics manufacturer, engineer, or maker, we tailor the best solutions for you. Visit our official website to embark on a new chapter of your design journey!