In the field of electronic manufacturing, the soldering process plays a crucial role in ensuring product quality and reliability. Hot Air Solder Leveling (HASL), as a common surface treatment technique, has been widely utilized in PCB manufacturing. This article will delve into the classification, pros and cons of the HASL process, as well as its applications in modern electronic manufacturing and potential challenges it may encounter.
HASL (Hot Air Solder Leveling) Overview
HASL (Hot Air Solder Leveling) is a thermal solder leveling process commonly used in electronic manufacturing, particularly in the surface treatment of Printed Circuit Boards (PCBs). This process involves coating solder (usually a tin/lead alloy) onto the PCB's solder pads, followed by melting the solder through heating and compressed air to create a smooth surface layer.
This helps enhance soldering quality, prevent oxidation, and provide reliable connections for assembling electronic components.
The HASL process can be applied to two different types of solder: Lead HASL and Lead-Free HASL. Lead HASL utilizes a tin/lead alloy, whereas Lead-Free HASL employs lead-free solder to comply with environmental regulations such as the RoHS standard.
Despite HASL having a long history in electronic manufacturing, with technological advancements, some new surface treatment processes have gradually been applied, such as Lead-Free HASL and Electroless Nickel Immersion Gold (ENIG).
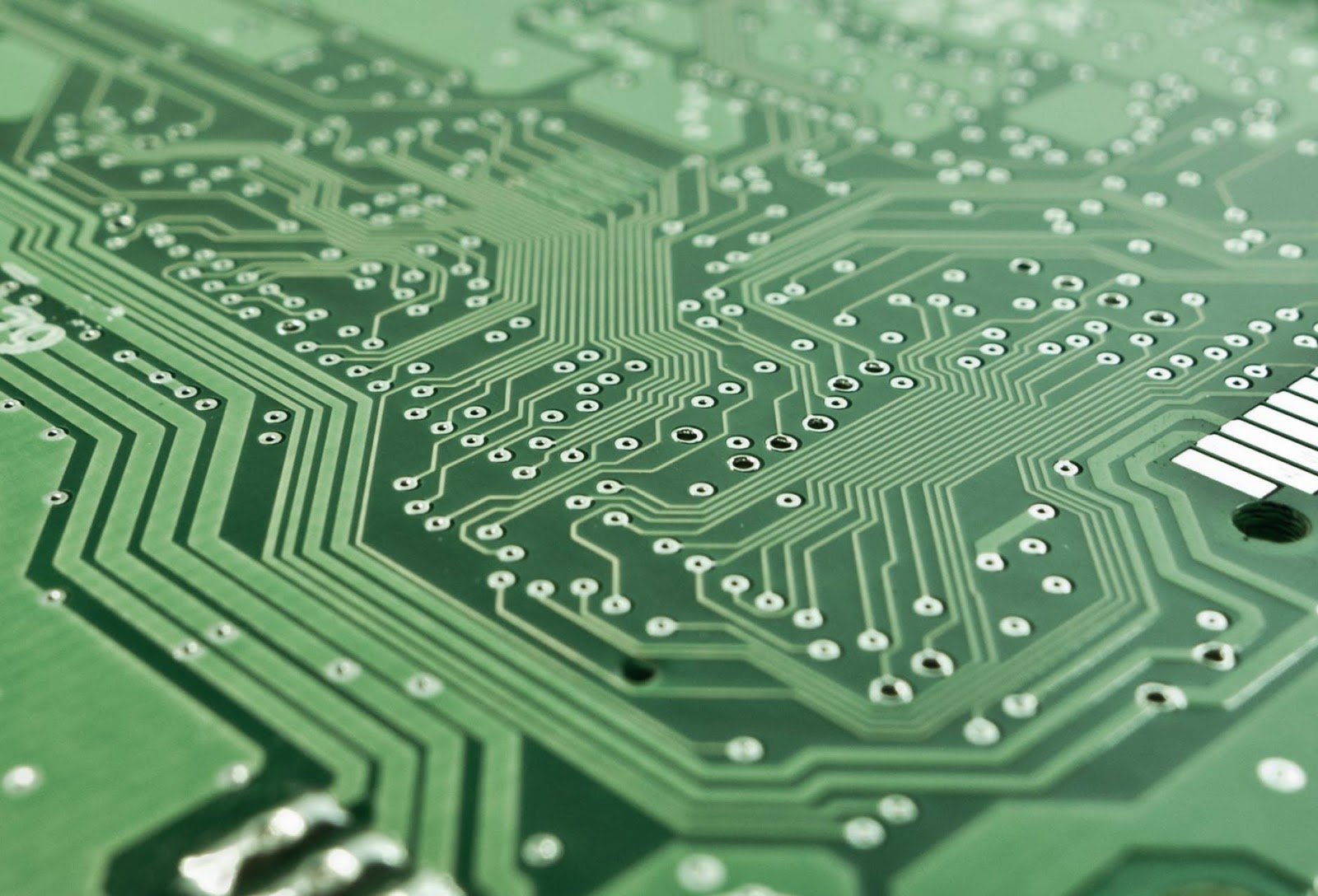
HASL (Hot Air Solder Leveling) Process Flow
Pad Preparation:
The first step in the HASL process involves the preparation of the pads. Pads are critical areas for connecting electronic components, and their surfaces must be carefully treated to ensure good soldering quality.
Typically, during the manufacturing process, the pad surfaces undergo a deoxidation treatment to remove surface oxides and impurities, thereby providing better solderability.
Coating Solder Paste:
After the preparation of the solder pads on the PCB surface is completed, apply molten Sn/Pb solder paste. This solder paste becomes liquid at high temperatures, allowing it to evenly coat the surface of the solder pads and fill the through-holes. The composition of the solder paste is crucial, as it directly affects the soldering performance and reliability.
Heating and Leveling:
Once the solder is applied to the pads and through-holes, the heating and leveling process begins. This typically involves using hot air or nitrogen to heat the solder, causing it to reach its melting point and become liquid. Simultaneously, compressed air is used to evenly distribute the solder, thereby achieving a flat surface. This process helps eliminate solder irregularities and ensures an even coating on the pad surfaces.
Formation of Copper-Tin Intermetallic Compounds:
During the solder liquefaction process, a reaction occurs between the tin in the solder and the copper on the solder pad, resulting in the formation of copper-tin intermetallic compounds (Cu-Sn). These intermetallic compounds exhibit excellent reliability and conductivity, enhancing the bonding strength and durability of the solder joint.
Cooling and Solidification:
After the heating and leveling process is completed, the solder gradually cools down and solidifies. This ensures that the solder can provide stable support and connections when joining components, thus ensuring the long-term reliability of the product.
Advantages of HASL (Hot Air Solder Leveling)
HASL (Hot Air Solder Leveling) has several notable advantages.
Low cost:
Compared to other complex soldering processes, the HASL technique is cost-effective and suitable for large-scale production.
Mature process:
HASL has been used in the electronic manufacturing field for many years, and its process is relatively stable and easy to master.
Strong oxidation resistance:
The solder-coated surface of the solder pad after HASL effectively prevents copper surface oxidation, thereby enhancing the reliability of solder joints.
Excellent solderability:
The surface after HASL has good solderability, which aids in soldering surface-mount components and other connections.
Disadvantages of HASL (Hot Air Solder Leveling)
However, the Hot Air Solder Leveling (HASL) process also has some disadvantages, which may become prominent in certain specific application scenarios.
Tombstoning Phenomenon:
After soldering, the surface of the solder pad may exhibit tombstoning, where the center of the pad sinks, potentially affecting solder joint reliability.
The root cause of tombstoning primarily lies in the uneven solidification contraction during the solder's cooling process, caused by surface tension of the solder. Factors such as uneven temperature distribution, solder composition characteristics, pad design, and improper process parameter control may lead to uneven contraction of the solder during cooling, resulting in a depression at the center of the solder, i.e., tombstoning.
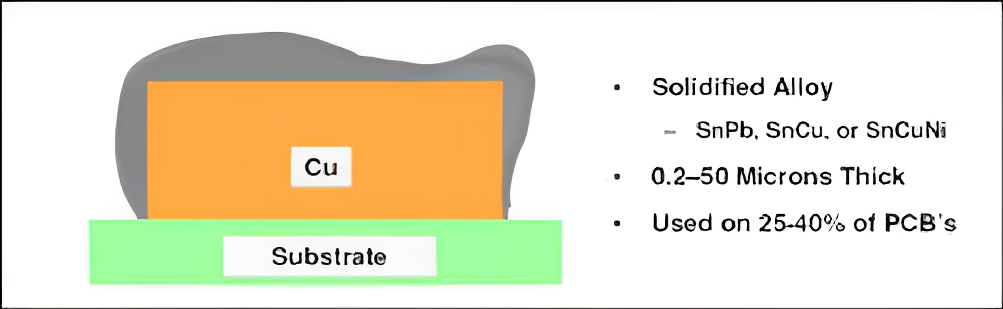
Insufficient Flatness:
The soldering process of the HASL technique may result in relatively lower flatness on the surface of solder pads, which could pose challenges for precise electronic component applications that demand high solder pad flatness requirements.
SMT Challenges:
For more precise solder pads, such as Ball Grid Arrays (BGAs), the Hot Air Solder Leveling (HASL) process may not be as suitable due to its higher surface tension, which could result in difficulties with component placement.
Application Areas of HASL (Hot Air Solder Leveling).
HASL has wide applications in the field of electronic manufacturing, particularly suitable for the production of mid-range and low-end electronic products, such as household appliances and consumer electronics. Its low cost and mature process provide a competitive advantage in large-scale production.
The HASL process is widely used in various sectors including household appliances, consumer electronics, LED lighting, industrial automation equipment, automotive electronics, and more.
household appliances
In the household appliance sector, electronic control boards and other electronic components often need to be soldered for products such as microwave ovens, refrigerators, and washing machines.
The low cost and mature process of Hot Air Solder Leveling (HASL) make it a common choice in the manufacturing of these products. Due to the relatively modest soldering requirements for these products, the HASL process can meet their reliability and performance needs.
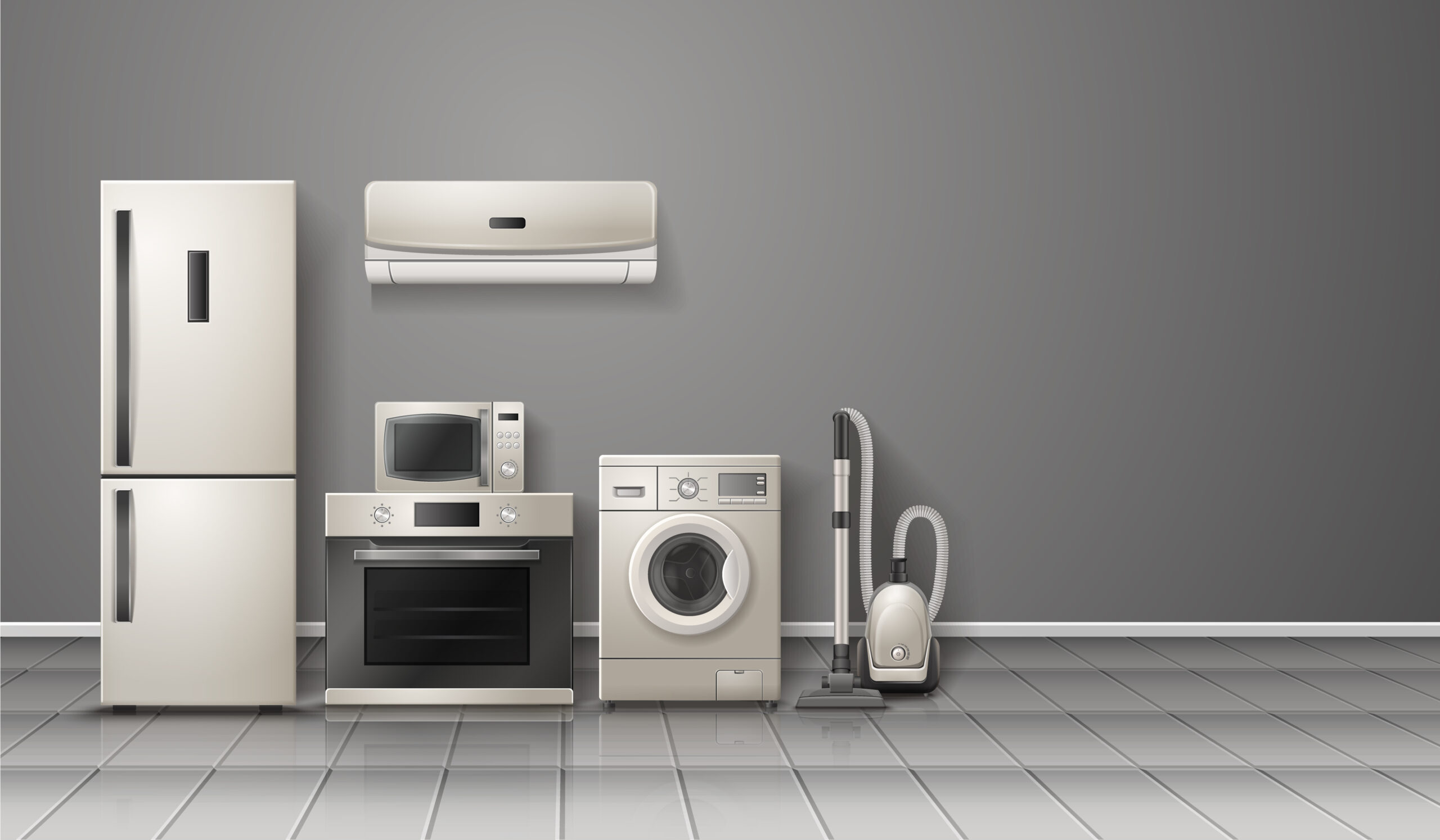
Consumer electronic products
Consumer electronic products such as mobile phones, tablets, and speakers require a significant number of electronic connections, including various components and connectors soldered onto circuit boards. Tin spraying technology is suitable for the manufacturing of these mid-to-low-end products, ensuring sufficient reliability while maintaining cost control.
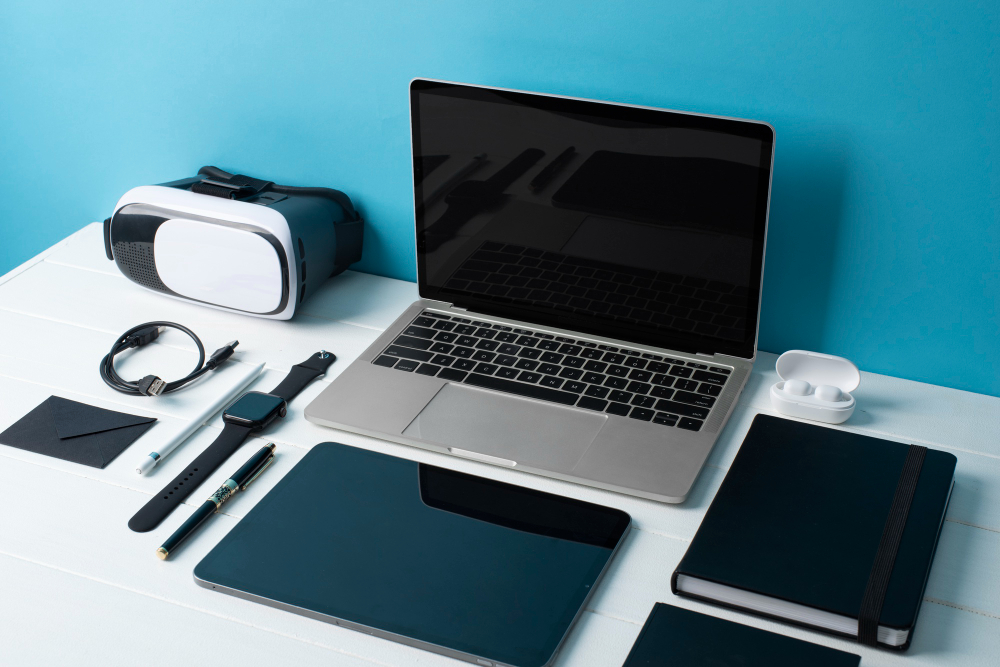
LED lighting products
LED fixtures typically include power circuits, driver circuits, etc., and these electronic components need to be soldered for connection. The anti-oxidation properties of the soldering process can effectively extend the lifespan of LED fixtures, while also meeting cost-effectiveness requirements.
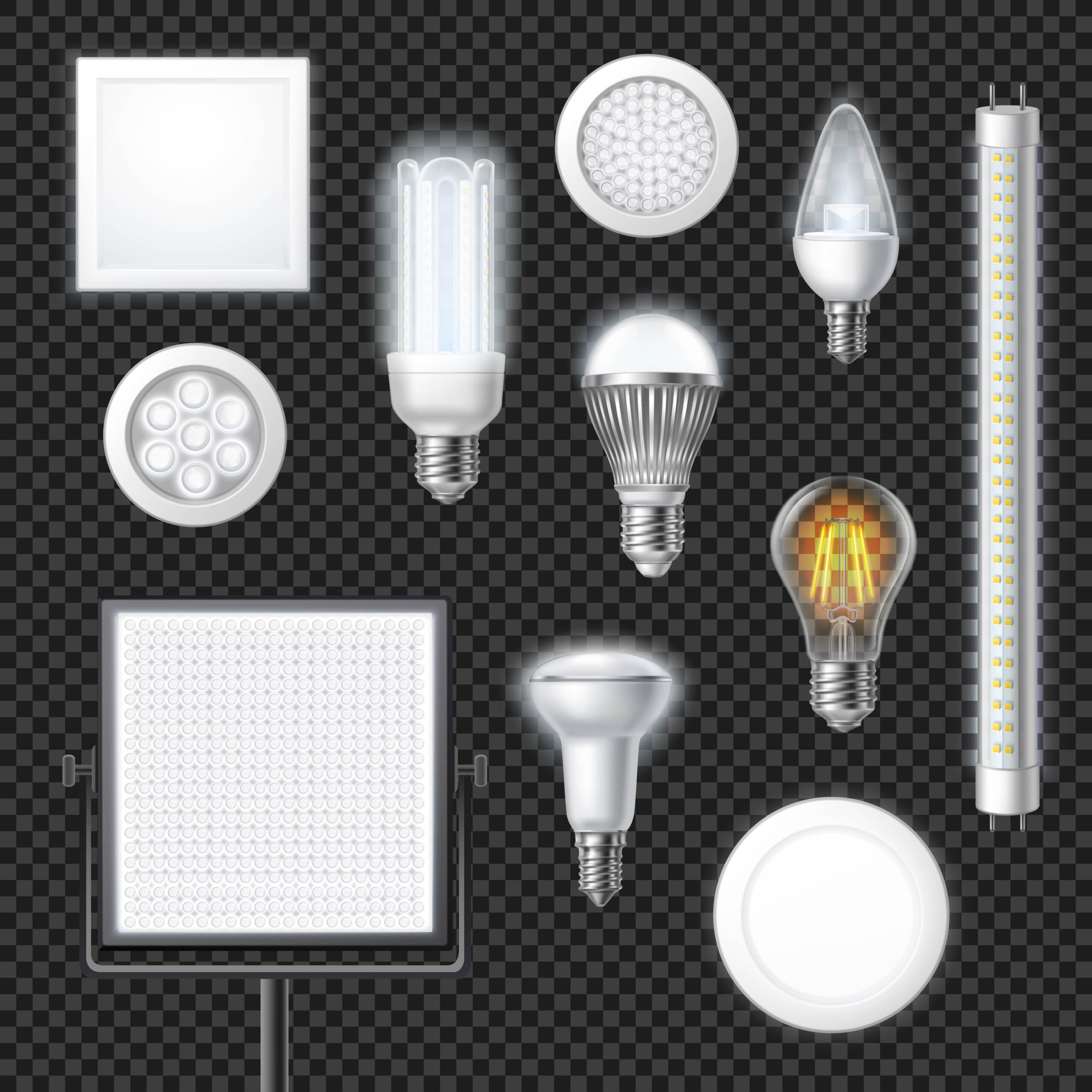
Industrial Automation Equipment
Control systems in industrial automation equipment often require soldering electronic components, such as PLCs (Programmable Logic Controllers), etc. The soldering process can provide cost-effective welding solutions for these devices, ensuring their stability and performance.
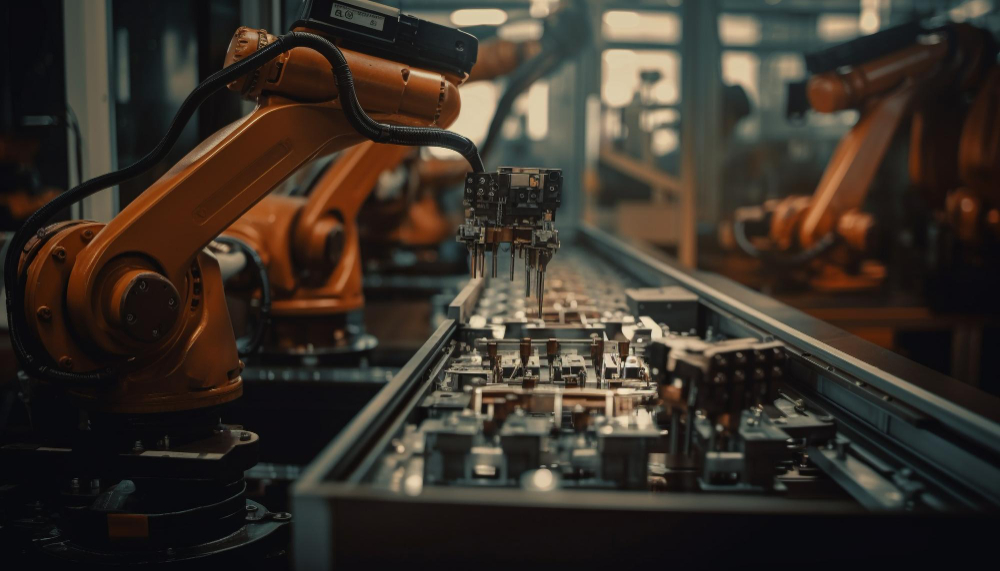
Automotive Electronics
Automotive electronics is also a crucial field of application. Modern vehicles involve a significant number of electronic control units and sensors, necessitating dependable electronic connections. For some mid-to-low-range automotive electronic products, the soldering process can meet their manufacturing requirements while reducing production costs.
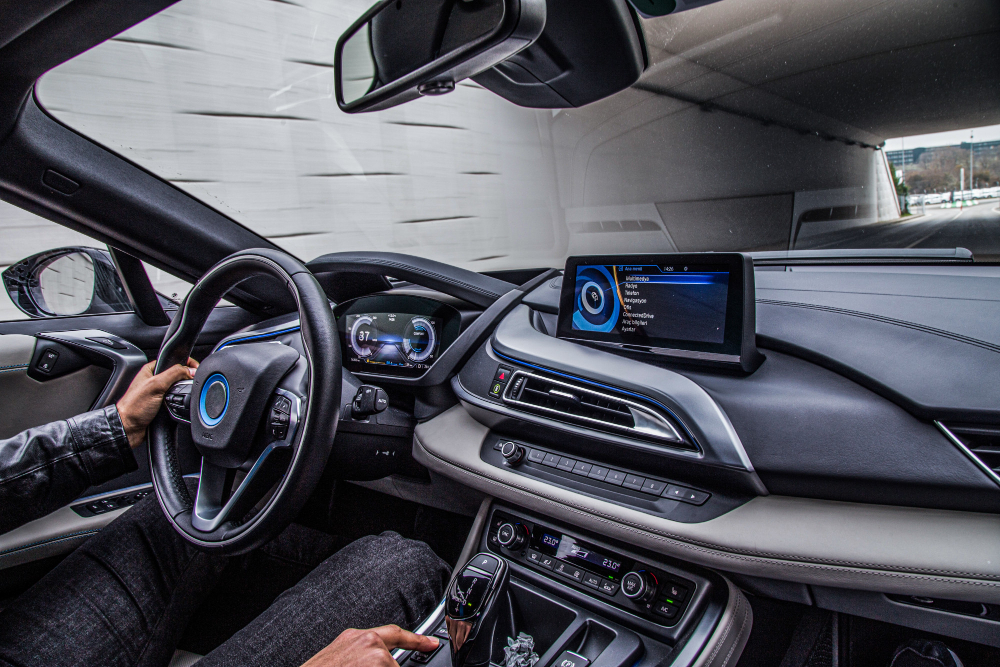
Challenges Faced by HASL (Hot Air Solder Leveling)
With the continuous development of electronic technology, the soldering process also faces certain challenges.
- As environmental regulations become increasingly stringent, the use of lead-free soldering will become a trend. However, its process parameters require higher levels of fine-tuning to ensure welding quality.
- Considering the characteristics of the soldering process, it is necessary to optimize the pad design to reduce occurrences of solder bridging, among other issues, and enhance solder joint reliability.
- For applications involving high-precision electronic components, improvements might be necessary in the soldering process to meet requirements such as pad flatness.
HASL, as a common surface treatment process, plays a significant role in electronic manufacturing. Its low cost and mature process give it an advantage in mass production, but it also requires optimization of pad design and process parameters to meet evolving electronic manufacturing needs. With environmental requirements and technological advancements, the spray tin process is expected to continue developing and expanding in the future.
With
SprintPCB's assistance, realizing your PCB design vision has never been easier. Whether you are a beginner or an experienced engineer, we can provide you with high-quality and efficient PCB manufacturing solutions. Visit our official website now to explore more about our services and let us collaborate to create your next remarkable project!