A backplane PCB is a special type of circuit board typically located at the back or bottom of electronic devices, designed to support and connect various electronic components and subsystems. Unlike regular PCBs, backplane PCBs have higher levels of complexity to accommodate a large number of connectors, slots, and other connecting devices. They also possess greater durability and stability to meet the demanding environments of electronic devices.
The design of backplane PCBs usually considers factors such as high-speed signal transmission, power distribution, thermal management, and EMI/EMC to ensure the stability and reliability of electronic devices. They can be single-layer,
double-layer, or
multi-layer structures, depending on the requirements and complexity of the device.
Main Functions of Backplane PCBs
Mechanical Support
Backplane PCBs provide a sturdy foundation for electronic devices, offering mechanical support and fixation to ensure the stability and safety of internal components.
Electrical Connections
The intricate circuit network on the backplane connects various electronic components, chips, modules, and other devices, enabling electrical connections and communication between different parts of the device.
Signal Transmission
Backplane PCBs are responsible for transmitting high-speed signals and data, ensuring fast and stable communication between components, which is crucial for the normal operation of the electronic device.
Power Distribution
Backplane PCBs handle power distribution and management, ensuring stable and reliable power supply to various components to meet the device's power consumption needs.
Thermal Management
Backplane PCBs assist in conducting and dissipating heat, helping to effectively remove heat generated within the device and preventing overheating that could damage electronic components.
EMI/EMC Control
The design of backplane PCBs takes into account electromagnetic interference (EMI) and electromagnetic compatibility (EMC), implementing measures to reduce the device's interference with its external environment, thus ensuring stability and reliability.
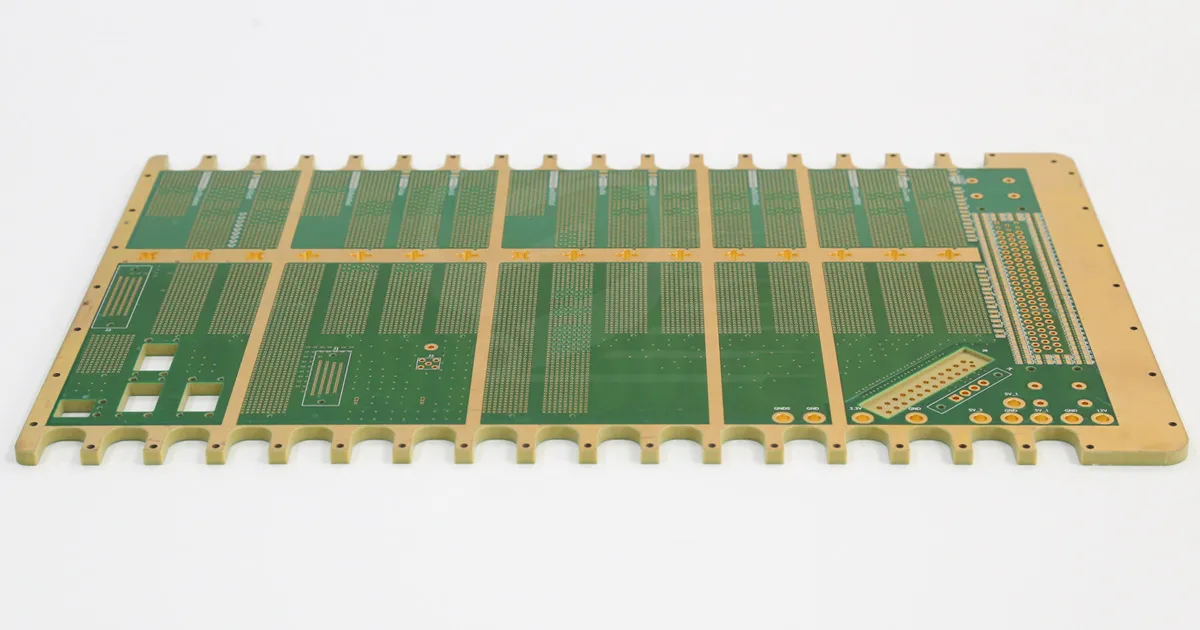
Features and Advantages of Backplane PCBs
Maintainability
Backplane PCBs are designed for easy maintenance and repair, utilizing modular designs and standard interfaces for convenient replacement and repair. For example, industrial control system backplanes use modular designs allowing quick replacement of faulty modules, reducing maintenance time and cost.
Enhanced Stability
High-quality materials and advanced manufacturing technologies ensure the stability and reliability of backplane PCBs, maintaining excellent performance even in harsh environments. For instance, military equipment backplanes use highly reliable materials and processes, undergoing rigorous testing and verification to ensure stability and reliability in battlefield conditions.
Assemblability
The design of backplane PCBs considers the need for assembly and integration, allowing flexible combination and assembly with other components to meet different equipment design requirements. For example, industrial automation equipment backplanes can be flexibly combined with various sensors, actuators, and other components to achieve complex control functions.
High Density
Backplane PCBs exhibit excellent high-density wiring capabilities, enabling the transmission and processing of numerous signals within limited space, meeting the high demands of modern electronic devices for data transmission speed and processing power. For example, server backplanes use high-density wiring designs to achieve high-speed transmission and processing of large volumes of data.
Functionality
Backplane PCBs can integrate multiple functions and communication interfaces to meet the functional requirements of different devices. For example, industrial control system backplanes integrate various communication interfaces and control functions, achieving complex control and monitoring capabilities.
Material Selection and Thickness Control
Backplane PCBs are generally thicker and heavier than regular PCBs, requiring strict material selection and thickness control. Choosing suitable base materials and copper cladding materials, such as FR-4, FR-5, and high-TG materials, and strictly controlling the thickness of the materials, help ensure the mechanical strength, thermal stability, and electrical performance of backplane PCBs. Additionally, considering the thermal expansion coefficient of the materials can prevent deformation or stress concentration during temperature changes, ensuring the stability and reliability of the circuit.
Inter-layer Alignment
Given the multiple layers and numerous drill holes in backplane PCBs, inter-layer alignment is a critical technique in the manufacturing process. High-precision lamination technology and advanced alignment equipment are used to ensure the accuracy and stability of inter-layer alignment.
Special Process Handling
The manufacturing process of backplane PCBs requires special treatments such as chemical copper plating, surface treatment, lamination, drilling, and electroplating. These processes need strict control to ensure the quality and stability of the backplane.
Thermal Management and Heat Dissipation Design
Due to the thickness and weight of backplane PCBs, heat dissipation and management are critical considerations in the manufacturing process. Utilizing heat sinks, heat sinks, fan cooling, and heat pipes, and selecting suitable heat dissipation materials, such as copper, aluminum, and thermal grease, can improve the thermal efficiency of backplane PCBs. Additionally, thermal simulation and testing should be conducted to evaluate the effectiveness of the heat dissipation design, ensuring the stability and reliability of the backplane.
Process Monitoring and Quality Control
During the manufacturing process of backplane PCBs, strict process monitoring and quality control are implemented to ensure that each step and process meet design requirements and standards. By establishing detailed manufacturing process specifications, regularly maintaining and calibrating production equipment, strictly controlling process parameters, monitoring and adjusting the manufacturing process in real time, and conducting rigorous inspection and testing of raw materials, processes, and finished products, the stability and reliability of the manufacturing process and the quality of backplane PCBs are ensured, thereby enhancing the competitiveness and market share of the product.