In the modern electronics industry, Printed Circuit Boards (PCBs) are crucial components. Whether it's a computer, smartphone, automobile, or any other electronic device, PCBs are used to support and connect electronic components. The design and manufacturing of PCBs play a vital role in the performance, reliability, and functionality of electronic devices.
The material selection for PCBs is one of the critical decisions that manufacturers must carefully consider during the design and production process. Different materials possess varying electrical, mechanical, and thermal properties, which directly impact the functionality and reliability of the PCB. Therefore, choosing the best PCB material is essential to ensure that the PCB meets the required performance in various application scenarios.
This article aims to explore how PCB manufacturers can choose the best PCB materials. We will begin by introducing the importance of PCB materials and their impact on electrical performance, mechanical performance, and thermal management.
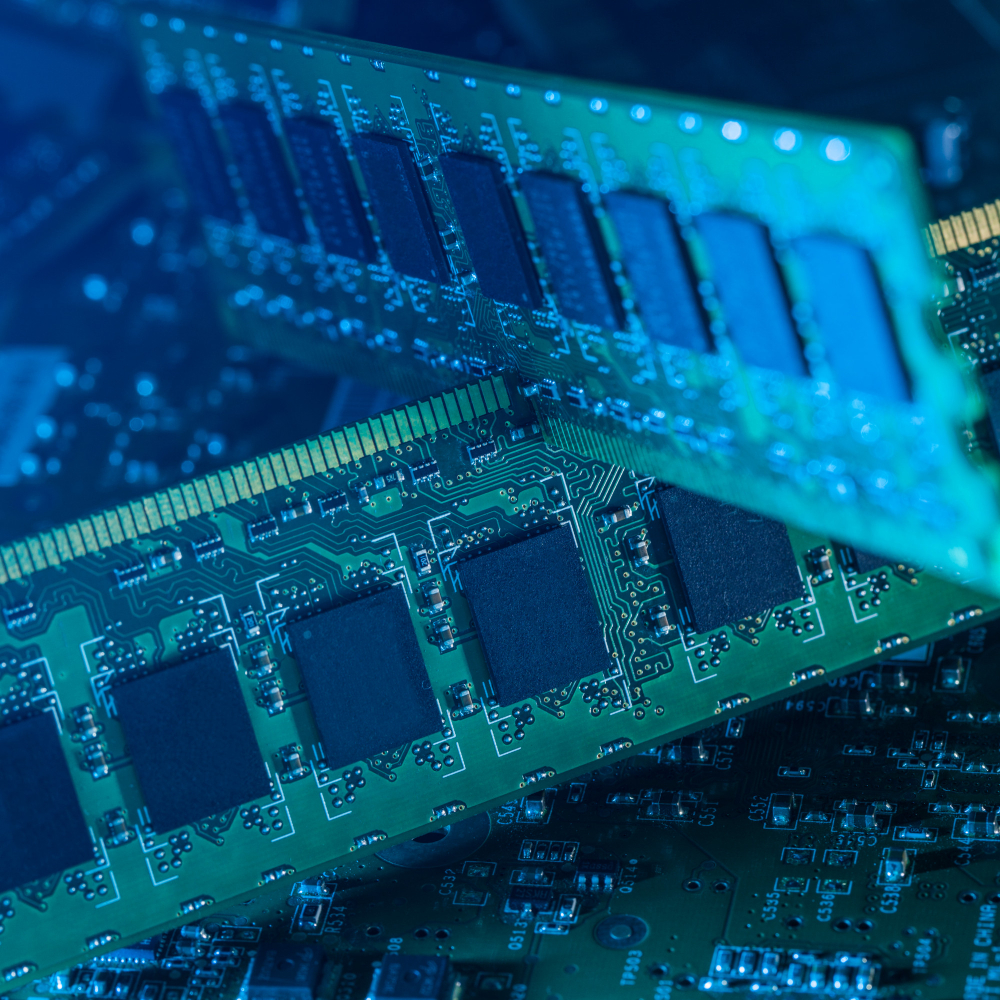
Then, we will delve into the key factors to consider when selecting PCB materials. Lastly, we will provide guidance on material selection and present case studies highlighting different material options.
The objective of this article is to offer valuable guidance and insights to PCB manufacturers, assisting them in making informed decisions regarding material selection.
The importance of PCB materials
Impact of PCB Materials on Electrical Performance
PCB materials are a crucial factor in determining the electrical performance of a circuit board. Different materials possess distinct electrical characteristics that can significantly influence the circuit's performance.
Dielectric Constant: The dielectric constant of PCB materials determines the propagation speed of signals on the board. A lower dielectric constant implies faster signal propagation, which is vital for high-frequency applications. Choosing materials with lower dielectric constants can reduce signal transmission delays and distortion.
Loss Factor: The loss factor measures the extent to which a material attenuates signals. A lower loss factor indicates that the material reduces energy loss during signal transmission, thereby preserving the signal's quality and strength. In high-frequency applications, selecting materials with lower loss factors can minimize signal attenuation and noise.
Electrical Insulation: PCB materials need to exhibit excellent electrical insulation properties to ensure proper isolation between different circuit layers or traces on the board. High-quality insulation materials prevent signal crosstalk and circuit short circuits, enhancing circuit stability and reliability.
Thermal Conductivity: The impact of PCB materials on thermal conductivity indirectly affects the electrical performance of the circuit. The material's thermal conductivity determines how heat generated in the circuit dissipates and spreads. Effective thermal management helps prevent component overheating, ensuring normal circuit operation and reliability.
Impact of PCB Materials on Mechanical Performance
In addition to electrical performance, PCB materials also significantly impact the mechanical performance and reliability of the circuit board.
Strength and Rigidity: PCB materials must possess sufficient strength and rigidity to withstand the stresses and vibrations during assembly and usage. Higher strength and rigidity prevent the circuit board from deforming, breaking, or getting damaged during operation.
Heat Resistance: PCB materials should exhibit excellent heat resistance to maintain the stability and reliability of the circuit board in high-temperature environments. In certain applications such as automotive electronics and aerospace, PCB materials must withstand extreme temperatures.
Chemical Resistance: PCB materials should have good resistance to common chemicals and environments. In some applications, especially in industrial or harsh environments, the circuit board may encounter corrosive gases, liquids, or chemicals. Choosing materials with excellent chemical resistance protects the circuit board from damage.
Impact of PCB Materials on Thermal Management
Thermal management is a crucial aspect of modern electronic device design, and PCB materials play a significant role in it.
Thermal Conductivity: The thermal conductivity of PCB materials determines the speed of heat propagation and dissipation on the circuit board. Excellent thermal conductivity helps quickly transfer heat from the circuit components to the surrounding environment, preventing component overheating and improving the overall system's thermal stability.
Coefficient of Thermal Expansion: The coefficient of thermal expansion of PCB materials refers to the material's dimensional changes with temperature variations. Selecting materials with a coefficient of thermal expansion matching other components reduces thermal stress and the risk of mechanical strain caused by thermal expansion and contraction, thereby lowering the risk of thermal failure in the circuit board.
Heat Dissipation Design: Different PCB materials have varying adaptability to heat dissipation designs and solutions. For high-power circuits, it may be necessary to choose materials with higher heat dissipation capabilities or implement heat-enhancing techniques such as thermal copper pads.
Essential Elements of PCB Materials
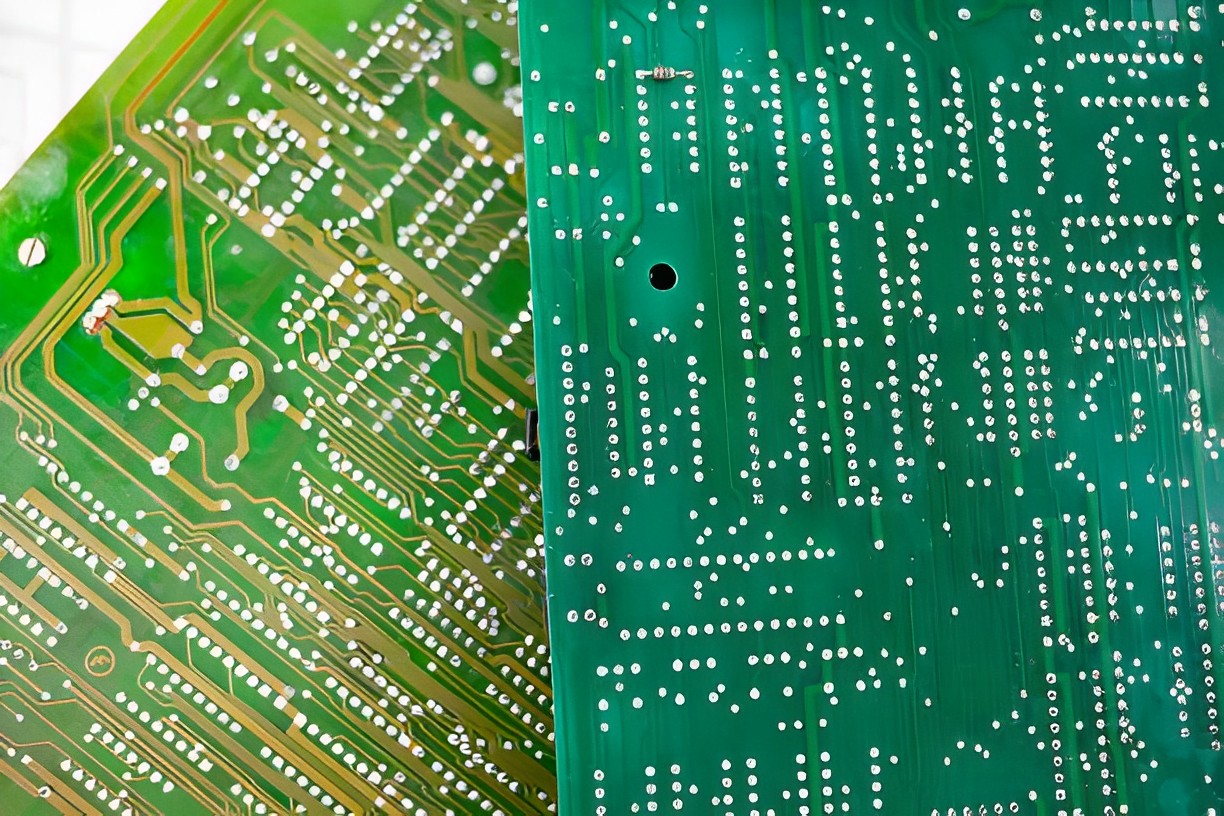
PCB materials are the fundamental components used in manufacturing Printed Circuit Boards (PCBs), and they directly impact the performance and reliability of the boards. In this section, we will discuss the essential elements of PCB materials, including conductivity, insulation, and thermal performance.
Conductivity:
Conductivity is a crucial characteristic of PCB materials as it determines the ability of signals to propagate through the circuit. Copper foils primarily provide conductivity in PCBs. Generally, copper foils with a thickness of 1 to 3 ounces are widely used in multi-layer PCBs. Thicker copper foils offer lower resistance and better conductivity.
However, using highly conductive copper foils also increases manufacturing costs, so it's necessary to strike a balance between cost and performance when selecting the thickness of copper foils.
Insulation:
Insulation is another key characteristic of PCB materials, ensuring that signals in the circuit do not experience interference or leakage. Common PCB materials like FR-4 (Fiberglass Reinforced Epoxy Laminate) exhibit good insulation properties. Insulation is measured by the material's dielectric constant and dissipation factor.
The dielectric constant represents the material's impact on the propagation speed of electromagnetic waves, while the dissipation factor reflects its energy absorption capacity. In high-frequency applications, materials with lower dielectric constants and dissipation factors should be chosen to minimize signal loss and interference.
Thermal Performance:
Thermal performance of PCB materials is vital for circuit reliability and stability. It primarily involves the material's thermal conductivity and glass transition temperature (Tg). Thermal conductivity determines how efficiently the material transfers heat and is particularly important for circuits requiring heat dissipation. Higher thermal conductivity helps maintain stable temperatures on the circuit board.
Tg refers to the temperature at which the material transitions from a glassy state to a rubbery state, reflecting its mechanical strength and dimensional stability at elevated temperatures. High-Tg materials can resist deformation and failure under high-temperature conditions, making them suitable for high-temperature applications.
In addition to conductivity, insulation, and thermal performance, other factors such as mechanical properties, chemical resistance, dimensional stability, and cost need to be considered.
The selection of the best PCB material should be based on a comprehensive assessment of application requirements, performance metrics, and cost-effectiveness. Industry standards and technical information provided by suppliers are valuable references for manufacturers when making material choices.
Criteria for PCB Manufacturers in Choosing the Best PCB Material
Researching and Understanding Specific Application Requirements
Before selecting the best PCB material, PCB manufacturers need to conduct in-depth research and understand the specific requirements of the application. Here are some important aspects to consider:
PCB Purpose and Operating Environment
Determine the intended application of the PCB, such as communication devices, medical equipment, automotive electronics, etc.
Analyze the environmental conditions in which the PCB will operate, such as temperature, humidity, corrosive gases, etc.
Complexity of the Circuit and Operating Frequency
Understand the complexity and hierarchical structure of the circuit, including the required number of layers and line width/spacing.
Determine the operating frequency range of the circuit, as high-frequency applications have higher demands on material electrical properties.
Critical Electrical and Mechanical Performance Indicators:
Consider electrical performance requirements, such as dielectric constant, loss tangent, controlled impedance, etc.
Understand mechanical performance requirements, such as flexural strength, impact resistance, surface flatness, etc.
Reliability Requirements
Determine the reliability requirements of the PCB within its expected lifecycle, such as durability, stability, and reliable connectivity.
Consider reliability requirements under specific stress conditions, such as vibration, temperature variations, and humidity variations.
By gaining a deep understanding of the specific application requirements, PCB manufacturers can lay the foundation for selecting suitable materials. This stage requires thorough communication and collaboration with customers, engineers, and design teams. Manufacturers can also refer to industry standards and guidelines, such as specifications and recommendations from the IPC (Association Connecting Electronics Industries), to learn about best practices in specific application domains.
After understanding the specific application requirements, PCB manufacturers can further weigh the pros and cons of different materials and choose the most suitable one to meet the design requirements.
This involves considering factors such as electrical performance, thermal performance, mechanical performance, cost, and availability of materials. Additionally, manufacturers can validate the performance and reliability of the selected materials through prototyping and conducting practical testing.
In summary, researching and understanding specific application requirements is a crucial step in choosing the best PCB material. It ensures that manufacturers can meet customer needs and produce PCBs with reliable performance.
Reference PCB Manufacturer Industry Standards and Guidelines
When choosing the best PCB material, PCB manufacturers can refer to industry standards and guidelines that provide valuable information about material performance and suitability. Here are some commonly used industry standards and guidelines for manufacturers to consider:IPC (Association Connecting Electronics Industries) standards and specifications:
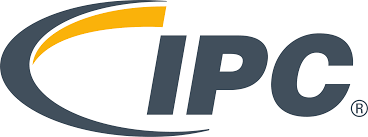
IPC-2221: Generic PCB design standard that provides guidance on trace widths, spacing, hole sizes, etc.
IPC-4101: Specification for PCB base materials, including performance requirements for materials like FR-4, CEM-1, PTFE, etc.
IPC-6012: Specification for rigid PCB quality and reliability, covering various aspects of PCB manufacturing.
IPC-6013: Specification for flexible PCB quality and reliability, applicable to flexible PCB manufacturing.
Technical documentation and recommendations from material suppliers:
PCB material suppliers typically provide technical datasheets and application guides that offer information on material properties, suitability, and processing recommendations.
Manufacturers can refer to material datasheets, technical manuals, and application guides provided by suppliers to understand the pros and cons of different materials and their applicable ranges.
Industry organizations and associations:
Industry organizations like the Institute of Electrical and Electronics Engineers (IEEE) and Electronic Industries Association (EIA) provide technical guidelines and research reports on PCB design and manufacturing.
Manufacturers can attend industry conferences, workshops, and training courses to network with peers, exchange experiences, and stay updated on industry trends and technological advancements.
Established design and manufacturing practices:
Learning from successful design and manufacturing cases helps manufacturers understand the types of materials and technology options used in similar applications.
Referring to past experiences and industry best practices can help manufacturers avoid potential issues and improve product reliability.
By referencing industry standards and guidelines, PCB manufacturers can access accurate information about the performance parameters, characteristics, and application ranges of different materials.
These guidelines assist manufacturers in better understanding the suitability of materials and providing guidance in selecting the best materials. However, manufacturers should also consider adjusting the standards and guidelines according to the requirements of specific applications to ensure that material selection aligns with their product's needs.
Actual Testing and Validation
Choosing the appropriate PCB material is a complex task because theoretical and technical data alone cannot fully predict how the material will perform in real-world applications. Therefore, PCB manufacturers typically conduct actual testing and validation to ensure that the selected material meets their requirements and expected performance.
Prototype Fabrication and Testing:
PCB manufacturers create prototypes using the selected material and evaluate its performance through a series of testing and validation procedures. These tests may include:
Electrical performance testing: Measuring the material's dielectric constant, loss tangent, dielectric strength, etc., to ensure it meets the signal transmission requirements of the circuit.
Thermal performance testing: Assessing the material's thermal conductivity, coefficient of thermal expansion, and Tg (glass transition temperature) to ensure reliability in high-temperature environments.
Mechanical performance testing: Testing the material's stiffness, impact resistance, creep resistance, etc., to ensure stability and reliability under mechanical stress.
Environmental adaptability testing: Exposing the prototype to different environmental conditions such as high temperature, low temperature, humidity, and chemicals to evaluate the material's resistance to aging and corrosion.
Reliability Assessment:
PCB manufacturers also conduct long-term reliability assessments of the selected material. This can involve accelerated life testing, thermal cycling testing, humidity-temperature cycling testing, etc., to simulate performance stability under actual operating conditions. These tests help manufacturers determine the material's lifespan, reliability, and predict potential issues that may arise during prolonged use.
Consideration of Cost and Processability:
During the actual testing and validation process, PCB manufacturers also evaluate the cost-effectiveness and processability of the selected material. Material cost may involve factors such as raw material procurement, processing and manufacturing costs, and subsequent maintenance costs.
Additionally, manufacturers consider the material's processability, including cuttability, drillability, lamination performance, etc., to ensure that the selected material is suitable for their production processes.
Through actual testing and validation, PCB manufacturers gain better insights into the real-world performance of the selected material and ensure it meets the requirements of their intended applications. This practice also helps mitigate risks and reduce production delays and cost losses caused by improper material selection. Furthermore, manufacturers can accumulate practical application experience, providing more accurate material selection recommendations for future projects.
While actual testing and validation may be time-consuming, they are critical steps in choosing the best PCB material. Through meticulous testing and validation, manufacturers can ensure that the selected material meets their specific requirements and delivers excellent circuit performance and reliability.
Case Studies of Common PCB Material Selection
In this section, we will discuss several case studies of common PCB material selections to help PCB manufacturers better understand how to choose the best materials to meet specific application requirements.
Low-Cost Applications: FR-4 and CEM-1
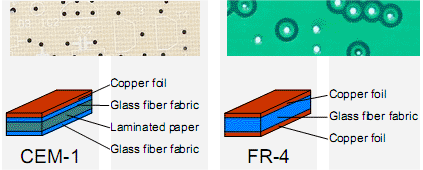
FR-4 is one of the most used PCB substrate materials. It offers good electrical performance, mechanical strength, and heat resistance. It is a fiberglass-reinforced epoxy resin-based material with a low price, suitable for general electronic products and low-cost applications.
CEM-1 is another common low-cost PCB material made of cellulose paper matrix and epoxy resin. It is inexpensive and suitable for simple single-layer or double-layer circuit boards.
High-Frequency Applications: PTFE and RF-35
PTFE is a commonly used material in high-frequency applications, known for its excellent dielectric performance and low loss characteristics. It provides low transmission loss and good signal integrity in the high-frequency range, making it suitable for wireless communications, radar, and satellite systems.
RF-35 is a specialized high-frequency material composed of ceramic-filled polymers. It has low dielectric constant and low dielectric loss, suitable for high-speed data transmission and high-frequency applications such as RF antennas and microwave circuits.
High-Temperature Applications: High-TG Materials and Ceramic Substrates
High-TG materials have a higher glass transition temperature (TG) and can maintain good performance stability in high-temperature environments. These materials are suitable for high-temperature applications such as automotive electronics, industrial controls, and aerospace systems.
Ceramic substrates are materials known for their high temperature resistance, mechanical strength, and excellent thermal conductivity. They are typically used in electronic power applications such as power modules, power amplifiers, and electric vehicle controllers.
Special Applications: Metal Core PCBs and Flexible PCBs
Metal core PCBs involve applying an insulating layer on a metal substrate and are used for heat dissipation and high-power applications. They exhibit excellent thermal conductivity and are suitable for high-power circuits such as LED lighting, power modules, and motor drivers.
Flexible PCBs are made of flexible polyimide (PI) or polyester (PET) materials, providing flexibility and foldability. They are suitable for applications with compact space, bending or folding requirements, such as wearable devices, mobile devices, and automotive interior electronics.
These case studies provide examples of common PCB material selections for different application scenarios. However, it is important to emphasize that each application has its specific requirements and constraints.
Therefore, when selecting PCB materials, it is crucial to consider factors such as application needs, performance specifications, cost, and availability. For specialized applications, further research and testing may be required to choose the best PCB materials.
In conclusion, PCB manufacturers need to consider various factors when choosing the best material for their PCBs. They should consider the requirements of the specific application, performance indicators, cost, and availability.
Referring to industry standards and conducting practical testing and verification can assist manufacturers in making informed decisions. With ongoing technological advancements and material innovations, PCB manufacturers will have more choices and opportunities to enhance circuit performance and reliability.
Elevate Your PCB Manufacturing with
SprintPCBSprintPCB stands as a prominent high-tech enterprise, delivering exceptional PCB manufacturing services to clients across the globe. With our extensive industry experience and competitive pricing, you can direct your focus towards the most crucial aspects of your organization. Contact us today to discover how we can collaborate and help you achieve your goals.