Surface finishing is a critical step in PCB manufacturing, directly influencing performance, reliability, and cost. Among the most common
PCB surface finishes are OSP (Organic Solderability Preservative), ENIG (Electroless Nickel Immersion Gold), and HASL (Hot Air Solder Leveling). Each finish is tailored for specific applications, offering unique advantages and challenges. This article provides a detailed exploration of these processes, focusing on their features, applications, costs, and impacts on soldering, reliability, and storage.
What is OSP (Organic Solderability Preservative)?
OSP is a water-based organic compound applied to PCB copper pads to prevent oxidation and ensure solderability. It acts as a temporary protective layer that can withstand thermal stress during assembly.
OSP Advantages:
OSP is cost-effective and environmentally friendly. It provides an extremely flat surface, making it ideal for high-density interconnect (HDI) designs and fine-pitch components. The application process is straightforward, involving no heavy metals, which ensures RoHS compliance.
OSP Limitations:
OSP has a limited shelf life and is sensitive to environmental factors such as humidity. Its solderability degrades after multiple thermal cycles, making it less suitable for complex assemblies requiring repeated reflow. Additionally, it offers limited mechanical protection compared to other finishes.
OSP Applications:
OSP is widely used in consumer electronics, such as smartphones, tablets, and gaming consoles, where cost and simplicity take precedence.
What is ENIG (Electroless Nickel Immersion Gold)?
ENIG is a two-layer finish featuring a nickel base layer topped with a thin layer of gold. The nickel provides a barrier to copper diffusion, while the gold layer enhances solderability and prevents oxidation.
ENIG Advantages:
ENIG offers a flat and smooth surface, making it highly compatible with HDI designs, ball grid arrays (BGAs), and surface mount technology (SMT). It provides excellent corrosion resistance and a long shelf life. ENIG’s dual-layer structure is robust, ensuring reliable solder joints and superior electrical performance.
ENIG Limitations:
ENIG is significantly more expensive than OSP or HASL due to its gold content and complex manufacturing process. Improper nickel plating can lead to black pad defects, a significant reliability concern.
ENIG Applications:
ENIG is the preferred choice for high-reliability industries such as aerospace, medical devices, automotive, and telecommunications. It is ideal for applications demanding precise signal transmission and durability.
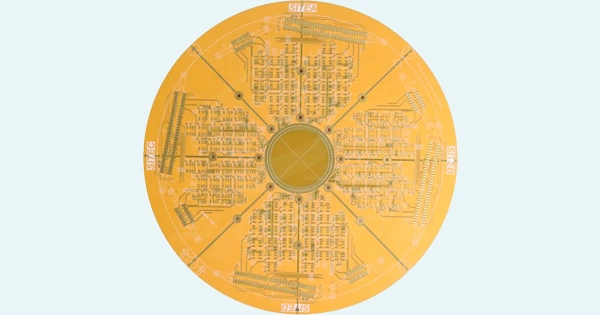
What is HASL (Hot Air Solder Leveling)?
HASL involves dipping the PCB into molten solder and using hot air to remove excess solder, leaving a uniform coating on the copper pads. It can be leaded or lead-free.
HASL Advantages:
HASL is cost-efficient and provides a thick, durable coating that protects copper from oxidation. Lead-free HASL variants align with environmental regulations, including RoHS compliance.
HASL Limitations:
HASL creates an uneven surface, which can be problematic for HDI designs and fine-pitch components. It is less suitable for modern PCBs requiring precise assembly. Traditional lead-based HASL is environmentally harmful, though lead-free alternatives mitigate this issue.
HASL Applications:
HASL is often used in industrial electronics, power supplies, and applications requiring robust mechanical connections.
Comparing PCB surface finishes: OSP, ENIG, and HASL
Cost Efficiency:
OSP is the most affordable surface finish, making it suitable for low-budget projects. HASL offers a middle-ground solution, balancing cost and durability. ENIG is the most expensive but provides unmatched performance and reliability.
Solderability and Reflow Tolerance:
ENIG excels in solderability, even after multiple reflow cycles. OSP is limited to one or two reflow processes, as its solderability degrades with repeated heating. HASL provides good solderability but struggles with high-density and fine-pitch designs.
Surface Flatness and Compatibility:
ENIG offers a perfectly flat surface, ideal for advanced designs like BGAs and SMT. OSP is flat but lacks the durability needed for high-stress applications. HASL’s uneven surface can hinder its compatibility with HDI designs.
Shelf Life and Durability:
ENIG boasts the longest shelf life and superior durability. HASL provides reasonable storage stability but requires careful handling. OSP has the shortest shelf life and is sensitive to environmental conditions.
Environmental Impact:
OSP and ENIG are environmentally friendly and lead-free. Traditional leaded HASL is harmful to the environment, though lead-free options address this issue.
Selecting the Right Finish for Your Application
The choice of surface finish depends on your project’s specific needs:
Choose OSP for cost-sensitive applications requiring simplicity and minimal thermal cycles.
Opt for ENIG when high reliability, flatness, and long shelf life are paramount.
Consider HASL for robust mechanical connections in industrial and less complex designs.
At SprintPCB, we offer a wide range of surface finish options tailored to meet your application requirements. Our advanced manufacturing capabilities ensure precise application and consistent quality, whether you choose OSP, ENIG, or HASL. With years of expertise in PCB production, we deliver solutions that balance performance, reliability, and cost.