In this era of rapid technological advancement, electronic devices are becoming smaller, lighter, and more flexible, making them increasingly convenient to carry around. In the midst of this wave of innovation, Flexible PCB (Printed Circuit Board) technology has emerged as a crucial component.
Its flexibility enables designers to incorporate more features and connections within complex and confined spaces. Therefore, it can be said that flexible circuit boards are the only solution to meet the demands of miniaturization and mobility in electronic products.
However, for many people, flexible PCBs still remain a relatively unfamiliar concept.
This article will take you on a quick journey to familiarize yourself with flexible PCBs and recognize their significance in modern electronic device design. Flexible PCBs are not just a technology; they are a key driving force behind innovation and advancement in electronic devices. Let's explore the fascinating world of flexible PCBs together!
First of all, we will provide a detailed explanation of the definition and basic concepts of flexible PCBs to help everyone gain a comprehensive understanding.
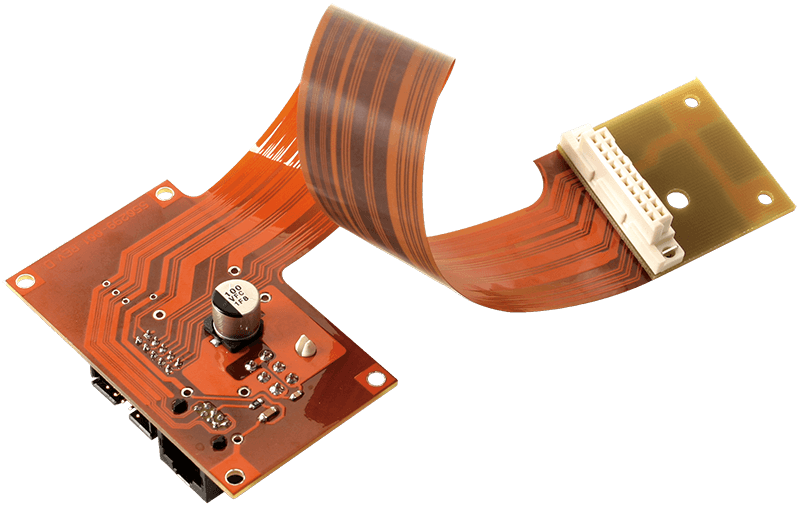
Flexible PCB (Flexible Printed Circuit Board) is a type of printed circuit board made from flexible base materials. It uses a flexible substrate, such as polyimide (PI) or polyester (PET), instead of the rigid board base used in traditional PCBs. Flexible base materials are typically high-temperature resistant and have good flexibility, such as polyimide (PI) or polyethylene naphthalate (PEN). The flexible substrate allows the PCB to work in shapes like bending, folding, and twisting.
"FPC" is the acronym for Flexible Printed Circuit, also known as "Flex PCB" in the industry. FPC is a type of printed circuit board made from flexible insulating materials. It is highly regarded for its lightweight, thin form factor, and exceptional characteristics like flexibility and foldability. FPC enables significant size reduction in electronic products, meeting the growing demand for high-density, miniaturized, and highly reliable devices.
Flexible Printed Circuit (FPC) is a technology that originated in the 1970s in the United States for the development of aerospace rocket technology. It is a type of printed circuit made from polyester film or polyimide as the base material, characterized by high reliability and excellent flexibility. By embedding circuit design on a flexible and thin plastic sheet, many precision components can be stacked in narrow and limited spaces, forming a flexible circuit that can be bent.This type of circuit can be bent, folded, lightweight, compact, has good heat dissipation, and is easy to install, breaking through traditional interconnection technologies. In the structure of flexible circuits, the materials involved are insulating films, conductors, and adhesives.Flexible PCBs are composed of one or multiple layers of thin film materials, with conductive layers or circuits coated on the areas where circuit connections are required. These conductive layers are typically made of copper foil and are formed into the desired circuit patterns through processes such as chemical etching or mechanical stripping. Flexible PCBs can also include circuit components, connectors, and other electronic elements.
Once we have understood the definition and basic concepts of flexible PCBs, let's talk about the common types of flexible PCBs.
Single-Sided Flex PCB(FPC)
The circuit on a single-sided flexible board is typically located on one side and uses copper foil as the conductive layer. The required circuit pattern can be created by chemical etching or mechanical removal methods. On the flexible substrate, protective layers or cover layers can be added to enhance the stability and durability of the circuit.
Single-sided flexible boards are widely used in low complexity and simple applications, especially in scenarios that require bending and compact designs. They can be utilized in various electronic devices such as wearables, mobile phones, digital cameras, printers, automotive electronics, and more.
Due to their advantages of flexibility and compact design, single-sided flexible boards have a broad range of applications in products that prioritize lightweight, flexibility, and reliability.
It is important to note that, due to having only one side available for circuit routing, single-sided flexible boards have lower circuit density and functional integration.
Double-Sided Flex PCB(FPC)
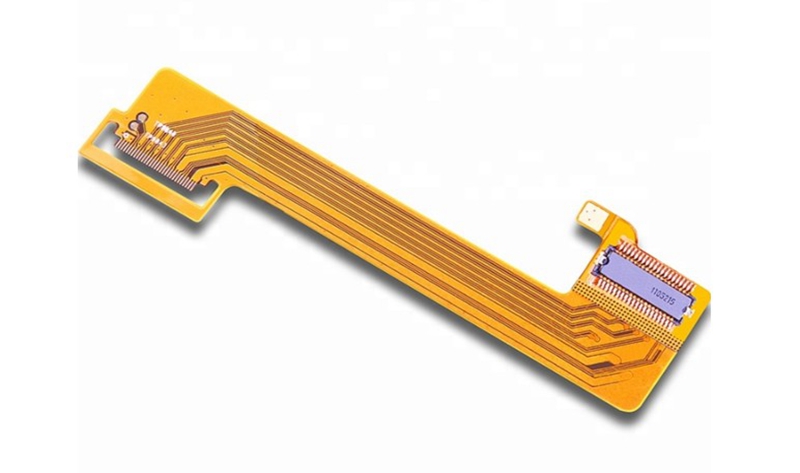
A double-sided flexible board consists of two flexible substrate layers sandwiching circuit layers. These circuit layers can be made of copper foil, which is formed into the desired circuitry and connection points through processes such as etching, punching, and electroplating. These substrates are capable of withstanding bending and stretching while maintaining the integrity of the circuit.
Both sides of a double-sided flexible board have circuit layers, allowing circuit routing and component assembly on both the top and bottom surfaces. This makes double-sided flexible boards more flexible and integrated compared to single-sided flexible boards. They can achieve more circuit connections and functional modules in small spaces while meeting requirements for high density and compactness.
Double-sided flexible boards are widely used in various fields. They are commonly found in consumer electronics, automotive electronics, medical devices, aerospace, and other industries where higher circuit density, reliability, and flexibility are required. The design and manufacturing requirements for double-sided flexible boards are high, involving considerations such as substrate selection, circuit design, process control, and reliability testing.
Multi-Layer Flex PCB(FPC)
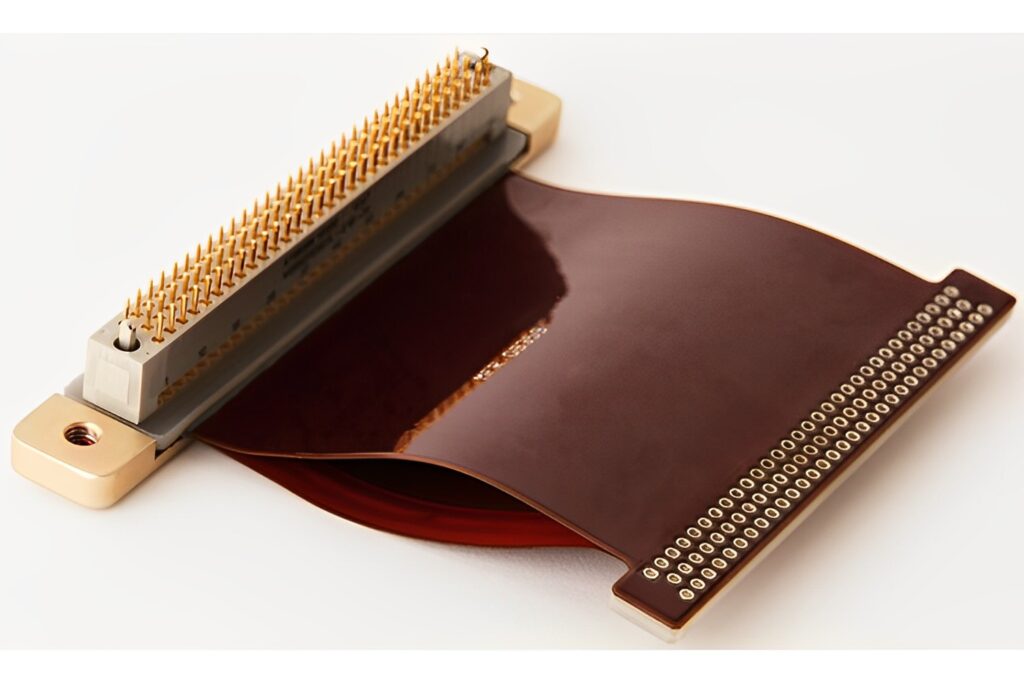
A multi-layer flexible board is a type of circuit board composed of multiple layers of flexible base material. It combines the flexibility of flexible PCBs with the structure of multi-layer circuit boards, providing both the bending and folding capabilities of flexible PCBs and higher circuit density and complexity.
Multi-layer flexible boards typically consist of three or more flexible layers, each containing circuit traces and components. These layers are electrically connected through interconnect holes (vias). The vias can be filled with copper by electrochemical deposition or include metal rivets to achieve the interconnection between circuit layers.
Special techniques and processes are required in the design and manufacturing of multi-layer flexible boards. Designers need to consider circuit layout, stacking order, and signal integrity between flexible layers to ensure the normal operation and stability of the circuits.
Multi-layer flexible boards play a significant role in many application areas, especially in fields that require high-density circuit connections, size constraints, and high reliability. They are widely used in wearable devices, medical instruments, automotive electronics, aerospace, and consumer electronics.
The advantages of multi-layer flexible boards include flexibility, thinness, good impact resistance, high circuit density, and strong resistance to interference. They provide greater freedom and reliability for innovative electronic product designs, while also improving the overall performance and reliability of the products.
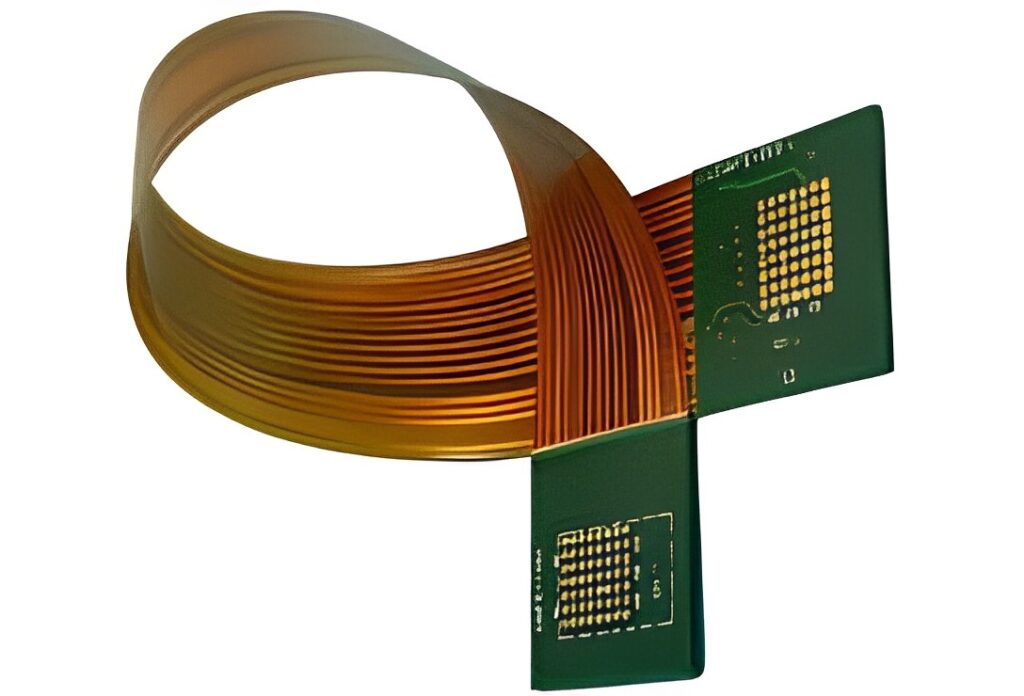
A rigid-flex PCB is a type of circuit board that combines the characteristics of rigid boards and flexible boards. It consists of rigid layers and flexible layers, enabling circuit connections through folding, bending, or twisting. The rigid-flex PCB merges the advantages of both rigid and flexible boards, offering flexibility, reliability, and suitability for applications that require complex layouts and three-dimensional designs.
Rigid-flex PCBs are typically composed of materials such as FR-4 for the rigid layers and polyimide or polyester for the flexible layers. The rigid layers are typically positioned at either end or in the middle of the PCB to provide support and protection for the circuit components, while the flexible layers are located in the connector areas or sections that require bending.
Next, we will tell you how to design flexible PCB.
How to design flex PCB?
The design of a flexible circuit board is based on the circuit schematic, with the goal of achieving the desired functionality as envisioned by the circuit designer. The main steps in the design process revolve around the layout design, considering multiple factors to ensure the effectiveness and reliability of the design. Here is a detailed explanation of the process involved in flexible circuit board design.
Goals of Layout Design: The layout design of a flexible circuit board aims to translate the circuit schematic into an actual circuit board layout that meets the functional requirements of the circuit designer. Through proper placement and interconnection, it ensures correct interconnectivity and signal transmission between circuit components.
External Connection Layout: In layout design, the layout of external connections needs to be considered, including input/output interfaces, power connections, communication interfaces, etc. The positions and routing of these external connection points should facilitate connectivity with other systems or devices.
Optimization of Internal Component Layout: In flexible circuit board design, optimizing the layout of internal electronic components is crucial. Arranging the components' positions to minimize circuit size and complexity maximizes circuit reliability and performance.
Optimization of Metal Traces and Via Layout: Flexible circuit board design also involves optimizing the layout of metal traces and vias. The paths of metal traces should be optimized to ensure signal transmission quality and reliability. The positioning and layout of vias need to consider the circuit connections between layers and ensure their reliability and performance.
Electromagnetic Protection: When designing flexible circuit boards, appropriate electromagnetic protection measures should be taken to minimize the impact of external electromagnetic interference on the circuit. This includes proper grounding layout, using shielding layers and ground planes to reduce electromagnetic radiation and sensitivity.
Thermal Dissipation Considerations: Thermal dissipation issues need to be considered in flexible circuit board design. Properly designing and placing heat dissipation areas ensures effective heat dissipation during high-power operation, avoiding circuit failures due to overheating.
Application of CAD Tools: For complex flexible circuit board designs, computer-aided design (CAD) tools are commonly used to assist in the process. These tools provide various functionalities such as layout design, routing planning, and signal integrity analysis, improving design accuracy and efficiency.
Through meticulous flexible circuit board design, circuit performance can be optimized, production costs can be saved, and reliable circuit and heat dissipation performance can be ensured. The design process needs to consider factors such as functional requirements, layout optimization, signal integrity, electromagnetic protection, and thermal dissipation, ensuring design reliability and stability.
Applications of Flex PCB
The unique characteristics of flexible PCBs have made them widely used in various industries and application fields. Here are some key application areas of flexible PCBs:
Wearable technology: Flexible PCBs (Printed Circuit Boards) play a crucial role in wearable technology. With their lightweight and flexible nature, flexible PCBs can seamlessly conform to the body's curves while providing the necessary circuitry connections and functionality support. Examples include smartwatches, health monitoring devices, and smart wearables.
Automotive Electronics: Flexible PCBs are increasingly important in the field of automotive electronics. Due to limited space and numerous curves in automobiles, flexible PCBs can efficiently utilize space while meeting complex circuitry connection requirements. They play a key role in automotive navigation systems, in-car entertainment systems, body control units, and dashboards.
Medical Devices: Flexible PCBs find extensive applications in the medical device industry. The flexibility of these PCBs allows them to adapt to complex shapes of medical equipment while providing stable and reliable circuitry connections. They are used in medical imaging devices, pacemakers, implantable sensors, and bio-monitoring devices, among others.
Aerospace: The use of flexible PCBs in the aerospace industry is on the rise. Aerospace applications demand strict requirements for weight and space, and the lightweight and flexible nature of flexible PCBs make them an ideal choice. They are used in flight control systems, satellite communication equipment, aviation instruments, and internal circuitry of spacecraft.
Other Industries: In addition to the sectors, flexible PCBs are also utilized in many other fields. For instance, they are used in consumer electronic products such as tablets, smartphones, foldable screens, and flexible displays. Furthermore, they play important roles in industrial automation, military and defense, communication devices, and the Internet of Things (IoT).
Overall, the application scope of flexible PCBs is extensive, covering every industry that requires flexible circuitry connections and miniaturized designs. They not only meet the demands of modern electronic devices for flexibility and reliability but also provide more possibilities for innovative product designs. With ongoing technological advancements, the application areas of flexible PCBs will continue to expand and diversify.
The future trends of flex PCB
Flex PCB, as an innovative electronic technology, is continuously evolving and advancing. Here are some future trends of flex PCB, providing insights into its potential development directions.
With progress in material science and nanotechnology, we can expect the emergence of new materials with special properties and adaptability for flex PCB manufacturing. These materials may include foldable, self-healing, high thermal conductivity, and high strength materials, enhancing the performance and reliability of flex PCBs.
One of the key characteristics of flex PCB is its bending and folding capability. In the future, with further advancements in foldable technology, we can anticipate wider applications of flex PCB in areas such as foldable electronic devices and wearable devices. This will bring about more flexible, portable, and multifunctional electronic products.
With the rapid development of the Internet of Things (IoT) and smart devices, the demand for flex PCB is also increasing. Future flex PCBs will focus more on enhancing intelligence and integration to meet the requirements of complex and highly integrated electronic systems. This includes integrating sensors, RF antennas, energy harvesters, and flexible displays.
Future flex PCBs will continue to evolve towards smaller and thinner form factors. As electronic devices trend towards miniaturization and micro-scale, flex PCBs will play a crucial role in enabling electronic components to adapt to smaller spaces and dimensional requirements. This will drive innovation and technological advancements in flex PCBs.
Environmental awareness and sustainable development are gaining widespread attention. Future flex PCB manufacturing will emphasize environmental friendliness and sustainability. This includes the use of eco-friendly materials, adoption of energy-efficient manufacturing processes, and promoting the application of circular economy models.
In summary, the future trends of flex PCB will showcase more innovations and breakthroughs in material advancements, foldable technology, intelligence, miniaturization, and sustainable development. This will bring greater flexibility, reliability, and performance to electronic device designs, driving technological development and innovation across various industries.
Through this blog article, we have learned an important lesson. We hope this blog post has been helpful to you and provided you with a comprehensive understanding and inspiration regarding flexible PCBs. Thank you for reading! If you have any questions or feedback, please feel free to
contact us. We wish you success in the world of flexible PCBs!